Miscalculating concrete quantities can lead to costly material shortages, delays, or excess waste—all of which impact project timelines and budgets. Concrete takeoff ensures that you order the exact amount needed for slabs, foundations, columns, and other structures, minimizing errors and preventing rework.
A well-executed concrete takeoff not only improves material efficiency but also helps contractors plan labor, equipment, and scheduling more effectively. This article breaks down the concrete takeoff process step by step, ensuring accurate estimates, reduced waste, and better project execution.
Read "A Comprehensive Guide to Material Takeoffs for Construction Projects" to understand material takeoffs.
What Is a Concrete Takeoff?
Concrete takeoff is the process of determining the exact amount of concrete needed for a construction project. It involves reviewing project plans, identifying concrete elements, and calculating their required volume. This step is important in estimating costs, ensuring material availability, and avoiding shortages or excess.
A concrete takeoff includes all types of concrete specified in the project, along with their required compressive strength, typically measured in pounds per square inch (PSI). The quantities are calculated in cubic yards to match industry standards. In addition to concrete, takeoffs have to account for other essential materials, including:
- Formwork to shape and support the concrete until it sets
- Reinforcing steel (rebar) to improve tensile strength
- Welded wire mesh for additional reinforcement
- Prestressed cables for structural stability
- Anchor bolts to secure structural components
- Vapor barriers to prevent moisture infiltration
Why Is an Accurate Concrete Takeoff Important?
A well-executed concrete takeoff prevents cost overruns by providing an accurate estimate of material quantities. Without this, you risk underestimating or overestimating the required concrete, both of which have financial consequences.
Underestimating leads to unexpected expenses and potential delays while waiting for additional material. Overestimating results in unnecessary costs, tying up funds that could be allocated elsewhere.
Material procurement becomes more efficient when takeoff calculations are precise. Ordering the correct amount of concrete reduces the chances of shortages that can halt work or excess material that increases waste and disposal costs.
Reliable estimates also allow suppliers to schedule deliveries according to the project timeline, ensuring a steady supply of materials without interruptions.
A detailed takeoff also improves overall project efficiency. It helps plan labor, equipment use, and scheduling by giving a clear picture of the concrete requirements. This allows contractors to coordinate different phases of construction, preventing bottlenecks and resource misallocation.
"Getting your concrete takeoff right isn’t just about numbers—it’s about keeping your project on track, cutting unnecessary costs, and avoiding last-minute surprises. A little extra accuracy now saves a lot of trouble later." - - Mauno Valli, Business Manager at Fondion
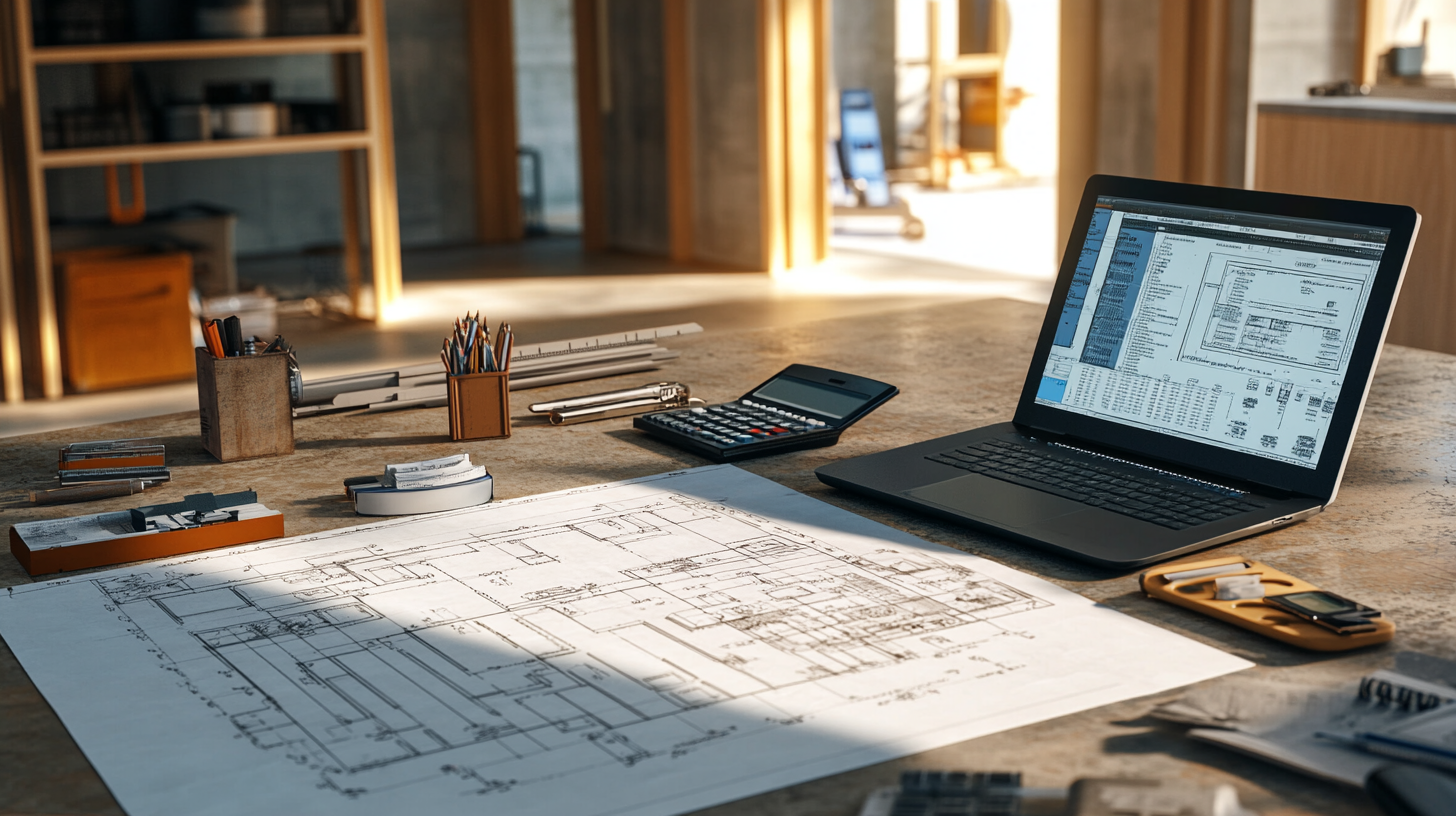
Step-by-Step Process for an Accurate Concrete Takeoff
1: Review the Construction Plans and Specifications
To perform an accurate concrete takeoff, start by thoroughly reviewing the construction plans and specifications. These documents contain critical details about the project, including dimensions, material requirements, and the overall scope of work.
Carefully analyzing them ensures that every concrete-related component is correctly identified and measured.
Pay close attention to the following aspects when reviewing the plans:
- Concrete types and quantities – Identify all required concrete types, including their compressive strength (measured in PSI) and the total volume needed, typically in cubic yards.
- Structural elements – Locate and account for foundations, slabs, footings, columns, and walls.
- Additional materials – Note the need for formwork, rebar, welded wire mesh, prestressed cables, anchor bolts, and vapor barriers, as these materials significantly impact cost and installation.
- Plan scaling and dimensions – Some project documents specify "do not scale drawings" to prevent measurement errors. In these cases, rely on written dimensions instead of scaling from the drawings. Always verify the scale on each plan sheet for accuracy.
- Inconsistencies and omissions – If discrepancies, missing details, or unclear specifications appear in the documents, consult the architect or engineer to clarify them before proceeding.
For general contractors, reviewing the entire project scope is important to ensure subcontractor estimates and bids align with the actual requirements. Concrete contractors should confirm the exact scope of work outlined in the bid invitation to avoid misestimating responsibilities.
2: Identify and Categorize Concrete Elements
Identifying and categorizing concrete elements is a key step in a concrete takeoff. This ensures that all necessary materials are accounted for and that estimates are accurate.
Start by identifying the different concrete components in the project. These typically include:
- Slabs: Horizontal surfaces like floors, pavements, and decks.
- Footings: Structural elements that distribute loads to the soil.
- Columns: Vertical supports that transfer loads from beams and slabs.
- Walls: Load-bearing or non-load-bearing structures made of concrete.
Once you have listed all the concrete elements, categorize them based on their function and specifications. Grouping elements by type helps prevent omissions and ensures that each component meets the project's design and strength requirements.
For each category, note the required concrete mix, compressive strength (measured in psi), and thickness specified in the project documents. This information is important for ordering the correct material and avoiding costly substitutions.
Check the plans and specifications carefully to confirm that all necessary details are accounted for. If any information is unclear, consult the architect or engineer before proceeding.
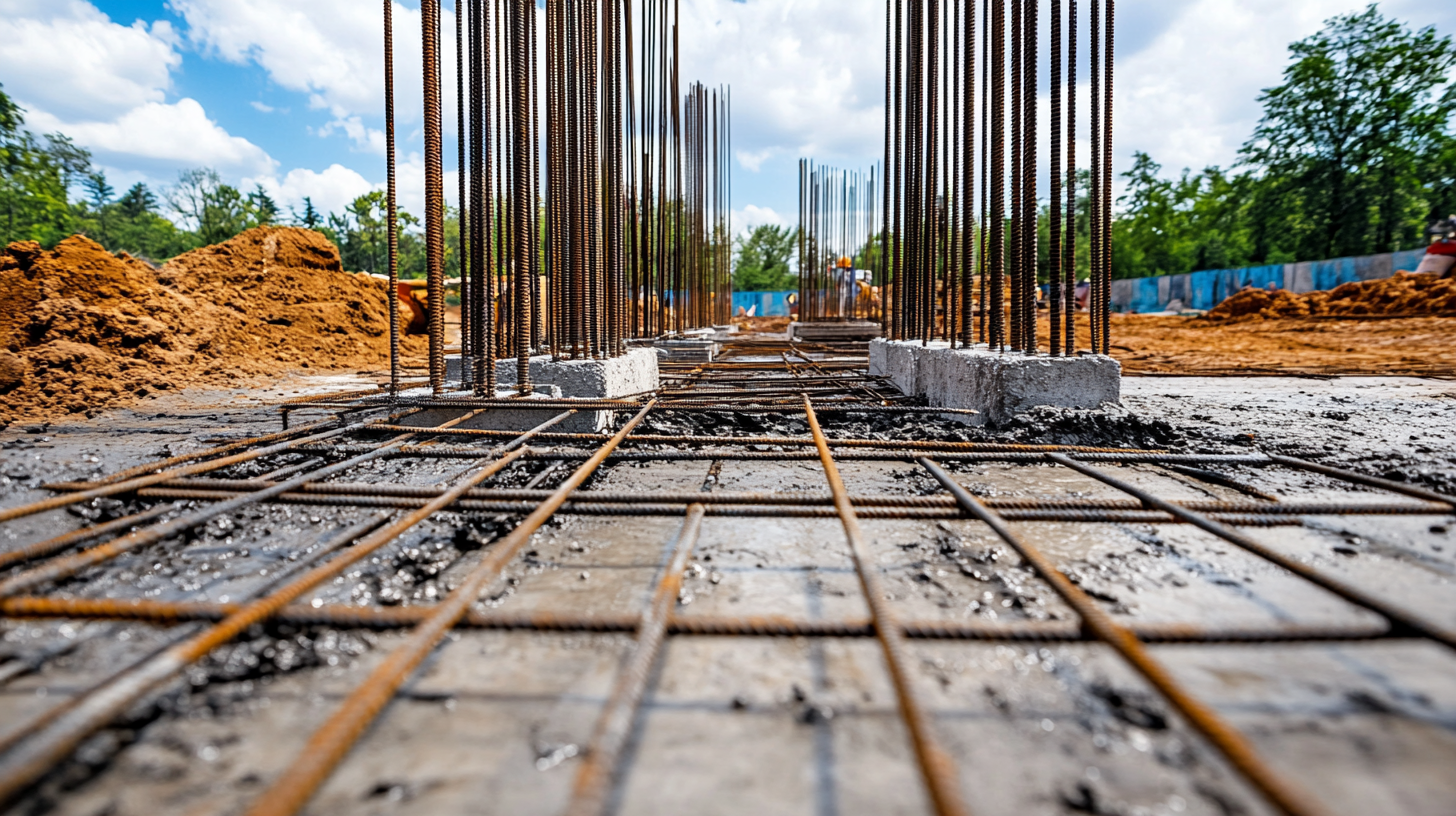
3: Measure and Calculate Concrete Volume
Accurate concrete takeoff starts with measuring the dimensions of each concrete element. You need to determine the length, width, and depth of every component, such as slabs, foundations, footings, and columns. These measurements form the basis for volume calculations, ensuring that the right amount of concrete is estimated.
Once you have the dimensions, use the appropriate formula to calculate the volume. The basic formula for volume is:
- Slabs and footings: Length × Width × Thickness
- Columns and piers: Base Area × Height
- Cylindrical elements: π × Radius² × Height
Since concrete is typically measured in cubic yards, convert the result from cubic feet by dividing by 27. For example, if a slab measures 20 feet long, 10 feet wide, and 0.5 feet thick, its volume calculation would be:
(20 × 10 × 0.5) ÷ 27 = 3.7 cubic yards
Always verify the scale on construction drawings before measuring. If the project specifies not to scale the drawings, rely on written dimensions instead. Double-check calculations to avoid ordering too much or too little concrete, preventing cost overruns or delays. Using digital takeoff tools can streamline this process, reducing errors and improving efficiency.
"Concrete takeoff isn’t just about crunching numbers—it’s about making sure every foundation, slab, and column is accounted for before the first pour. A small miscalculation here can mean big delays and extra costs down the line." - - Sanni Bomberg, Product specialist at Fondion
4: Factor in Reinforcements and Formwork
Reinforcements and formwork are important for both structural integrity and accurate material estimation in a concrete takeoff. Reinforcements such as rebar and welded wire mesh strengthen the concrete, preventing cracks and improving load-bearing capacity.
To account for them in your takeoff, review the project specifications to determine the type, size, and quantity of reinforcement required. Consider the following:
- Rebar: Identify the diameter, spacing, and placement based on structural drawings. Factor in lap splices bends, and waste.
- Welded Wire Mesh: Note the gauge, sheet size, and overlap requirements.
- Prestressed Cables: If applicable, account for their length and anchoring details.
- Anchor Bolts: Include their size, type, and locations based on foundation and slab plans.
Formwork is another important component, as it shapes and supports the concrete until it hardens. Neglecting formwork in your takeoff can lead to underestimated labor and material costs. Consider:
- Material Type: Determine whether the project requires plywood, steel, or plastic formwork.
- Surface Area: Calculate the total square footage of formwork needed for walls, slabs, and columns.
- Bracing and Supports: Include shoring, ties, and fasteners necessary for structural stability.
- Labor Requirements: Factor in the time and effort needed to assemble, disassemble, and potentially reuse formwork.
By including reinforcements and formwork in your takeoff, you ensure a more complete and accurate estimate, helping prevent shortages and unexpected costs during construction.
5: Account for Waste, Over-Excavation, and Site Conditions
Concrete quantity estimates have to account for material waste, site conditions, and over-excavation. Failing to include these factors can lead to shortages or excess material, increasing costs and delays.
Material waste occurs because of several factors:
- Spillage during mixing, transportation, and pouring.
- Batching errors, where incorrect proportions lead to unusable concrete.
- Pump and chute losses, as some material remains in equipment.
To minimize waste, calculate a contingency percentage—typically 5-10%—based on project complexity. For large pours, coordinate deliveries to reduce leftover material.
Site conditions also impact concrete requirements. Uneven terrain might require additional leveling or concrete volume adjustments. Soil stability influences the need for deeper footing or reinforced foundations. Weather conditions, such as high temperatures, can increase evaporation losses, requiring water adjustments or curing measures.
Over-excavation results in a larger-than-planned foundation or footing area. If not accounted for, it can lead to a concrete shortage. To compensate, verify excavation depths and widths before pouring and adjust estimates accordingly.
6: Use Takeoff Software for Accuracy and Efficiency
Takeoff software helps eliminate errors in concrete takeoff by automating measurements and calculations. Manual calculations can lead to mistakes in dimensions, unit conversions, or waste factors, which result in costly material shortages or overruns.
Digital tools allow you to set the correct scale, extract measurements directly from plans, and apply formulas automatically. This ensures accuracy and consistency in every estimate.
Fondion simplifies the concrete takeoff process by providing automated calculations, accurate quantity tracking, and seamless integration with estimating tools. With Fondion, contractors can reduce manual errors, optimize material planning, and ensure precise cost estimation, helping projects stay within budget and on schedule. Explore how Fondion can improve your takeoff process.
Automation also improves efficiency by reducing the time needed to perform a takeoff. Instead of manually measuring and recording dimensions, you can use digital tools to point, click, and drag to calculate quantities instantly.
Many takeoff programs also allow you to store project templates, reuse previous takeoffs, and integrate with estimating software to streamline the entire bidding process. By using digital takeoff tools, you can complete estimates faster and with greater confidence, reducing delays and improving project planning.
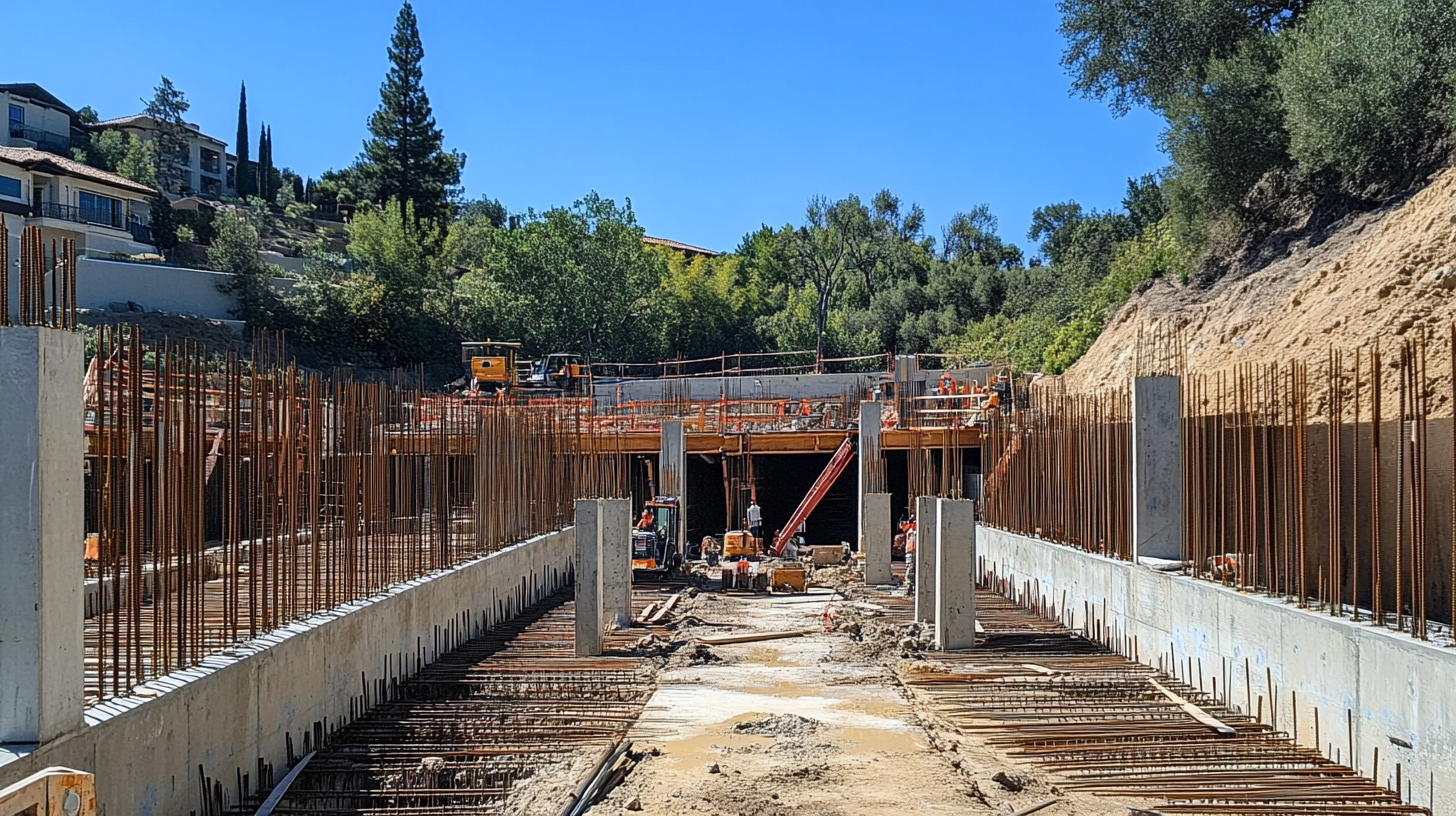
Common Mistakes to Avoid in Concrete Takeoff
Errors in concrete takeoff can lead to inaccurate material estimates, budget overruns, and project delays. Avoiding common mistakes ensures that you order the right amount of concrete and stay within budget.
Failing to thoroughly review construction plans often results in missed or incorrect concrete quantities. Every detail in the plans matters, from dimensions to material specifications. To prevent errors, always check for scaling instructions—some drawings specify "do not scale," meaning you have to rely on written dimensions instead. If any part of the plan seems unclear, verify details with the architect or engineer before proceeding.
Miscalculating concrete volume is another frequent mistake. Incorrect formulas or neglecting variations in shape can lead to underestimations or excess material. Use the correct formula for volume: length × width × thickness, then divide by 27 to convert cubic feet into cubic yards. For irregular shapes, break them down into simpler sections and calculate each separately. Double-checking your calculations and using digital takeoff tools can improve accuracy.
Not accounting for waste, over-excavation, and site conditions can create material shortages or unnecessary excess. Concrete waste occurs because of spillage, formwork leaks, and leftover material in mixing trucks. To compensate, include a waste factor—typically 5% to 10%—in your takeoff. Site conditions such as soil type and weather can also impact concrete needs. If over-excavation is required because of unstable ground, adjust the estimated volume accordingly.
Using takeoff software like Fondion can help minimize errors and streamline the estimating process. Digital tools allow you to set the correct scale, automate measurements, and factor in material costs. However, relying only on software without verifying inputs and outputs can still lead to mistakes. Always cross-check measurements manually when possible.
Conclusion
Accurate concrete takeoff is important for cost control, material planning, and project efficiency. Even small miscalculations can lead to budget overruns and delays. Using a structured approach and utilizing takeoff software improves precision and saves time.
Consistency and attention to detail make the difference between a smooth project and unexpected challenges. Investing in accuracy upfront leads to better project outcomes and fewer costly surprises.
Optimize Your Concrete Takeoff Process with Fondion
Fondion is a construction takeoff software designed to streamline the concrete takeoff process, ensuring accurate material estimates, reduced waste, and improved cost control. By automating calculations and integrating with estimating tools, Fondion helps contractors save time, minimize errors, and enhance project efficiency.
Start your free Fondion trial today and take the guesswork out of your concrete takeoff.
FAQ
What Is a Concrete Takeoff?
A concrete takeoff estimates the amount of concrete needed for a project by measuring slabs, footings, and columns from blueprints. It helps with budgeting, minimizes waste, and ensures efficient planning.
What Is the Easiest Way To Remove Concrete?
Use a jackhammer or sledgehammer for small areas and a concrete saw for precise cuts. For large-scale removal, heavy machinery may be needed. Always wear protective gear and check for rebar or utilities before starting.
How can I streamline concrete takeoff and cost estimation across multiple systems?
Make sure that you don’t have to manually enter data into different systems, but rather, you can manage all information from a single system. If you are using various systems, the system you choose, like Fondion, should act as the master. This way, you only need to set up projects in one software, which then syncs with other systems. This allows you to accurately estimate and monitor costs while ensuring that you can learn from historical data about your true costs, optimizing your operations for profitability across different areas.
How To Do a Concrete Wall Takeoff?
Measure the wall’s length, height, and thickness to calculate volume in cubic yards. Include rebar, formwork, and waste factors. Use takeoff software or manual calculations for accuracy and verify specifications before ordering.
What Is the Pull-Off Method of Concrete?
It tests the bond strength of concrete layers or coatings by applying tensile force to a metal disc attached to epoxy. The force needed to detach the disc indicates adhesion strength and surface preparation quality.
How Do I Calculate Concrete for Footings?
Multiply footing length × width × depth to get the volume, then convert cubic feet to cubic yards by dividing by 27. Add 5–10% extra for waste to ensure accurate ordering and avoid shortages. Good construction estimating software creates professional tender documents automatically and with the right content. In that way, you can make sure that you win more projects and have better profit margins because the documents automatically create a detailed list of what is included in the project and what is not included in the project. This way customer satisfaction stays very high while simultaneously you’ll only do the work that you are supposed to do keeping your time schedule and costs on budget.