Getting a roofing takeoff right can make or break a project. Roofing materials are sold in specific units, such as squares or bundles, and any miscalculation can lead to costly shortages or excessive waste. Underestimating materials cause delays, as additional orders may take time to arrive, disrupting project timelines.
Overestimating, on the other hand, ties up capital in unused materials that may not be returnable. Precision in takeoff calculations ensures that the right amount of materials is ordered, minimizing waste and controlling costs.
A proper roofing takeoff involves more than just measuring dimensions. It requires precise calculations for materials, accounting for slopes, waste factors, and special roof features like skylights or chimneys. Even small miscalculations can lead to significant financial losses and construction inefficiencies. This article covers essential tips for performing an accurate roofing takeoff to improve construction efficiency and ensure project success.
Discover more about material takeoffs in "A Comprehensive Guide to Material Takeoffs for Construction Projects."
What is Roofing Takeoff?
A roofing takeoff is the process of determining the materials needed for a roofing project. It involves calculating the quantity of shingles, underlayment, flashing, fasteners, and other essential materials based on the roof’s measurements and design. This step is important for ensuring that the right amount of materials is ordered before construction begins.
Roofing takeoff plays a key role in construction planning. It allows you to estimate costs accurately, helping prevent budget overruns. By determining material needs in advance, you can also avoid delays caused by shortages or miscalculations.
On the other hand, ordering too much material leads to unnecessary expenses and excessive waste, which can impact overall project efficiency.
By conducting a precise roofing takeoff, you improve both cost control and workflow efficiency. It ensures that workers have the necessary materials on hand, reducing downtime and keeping the project on schedule.
"Getting a roofing takeoff right means more than just measuring the roof. You have to factor in slopes, waste percentages, and material requirements to avoid costly miscalculations. A small error can lead to delays or wasted materials, so careful planning and accurate calculations are essential for a smooth project." - - Jarmo Valli Product Manager at Fondion
Key Components of a Roofing Takeoff
The primary materials for a roofing takeoff include:
- Shingles or roofing panels – The main covering material, such as asphalt shingles, metal panels, or tiles.
- Underlayment – A protective layer beneath the shingles that improves waterproofing.
- Flashing – Metal strips used around roof edges, chimneys, and vents to prevent leaks.
- Fasteners – Nails, screws, or other hardware to secure roofing materials.
- Ventilation components – Ridge vents, soffit vents, and other airflow solutions to prevent moisture buildup.
Measuring roof dimensions accurately is important for material estimation. You need to determine the length and width of each roof section and then calculate the total surface area. Roof slopes affect material requirements, so account for the pitch to ensure the correct amount of shingles or panels.
Waste factors also impact material calculations. Cutting materials to fit roof edges, valleys, and penetrations generates waste. Overlaps in underlayment and shingle placement further increase material use.
To compensate, add a percentage to your material estimate based on roof complexity. For simple roofs, a 5% waste factor might be enough, while complex designs with multiple valleys and dormers might require 10% or more.
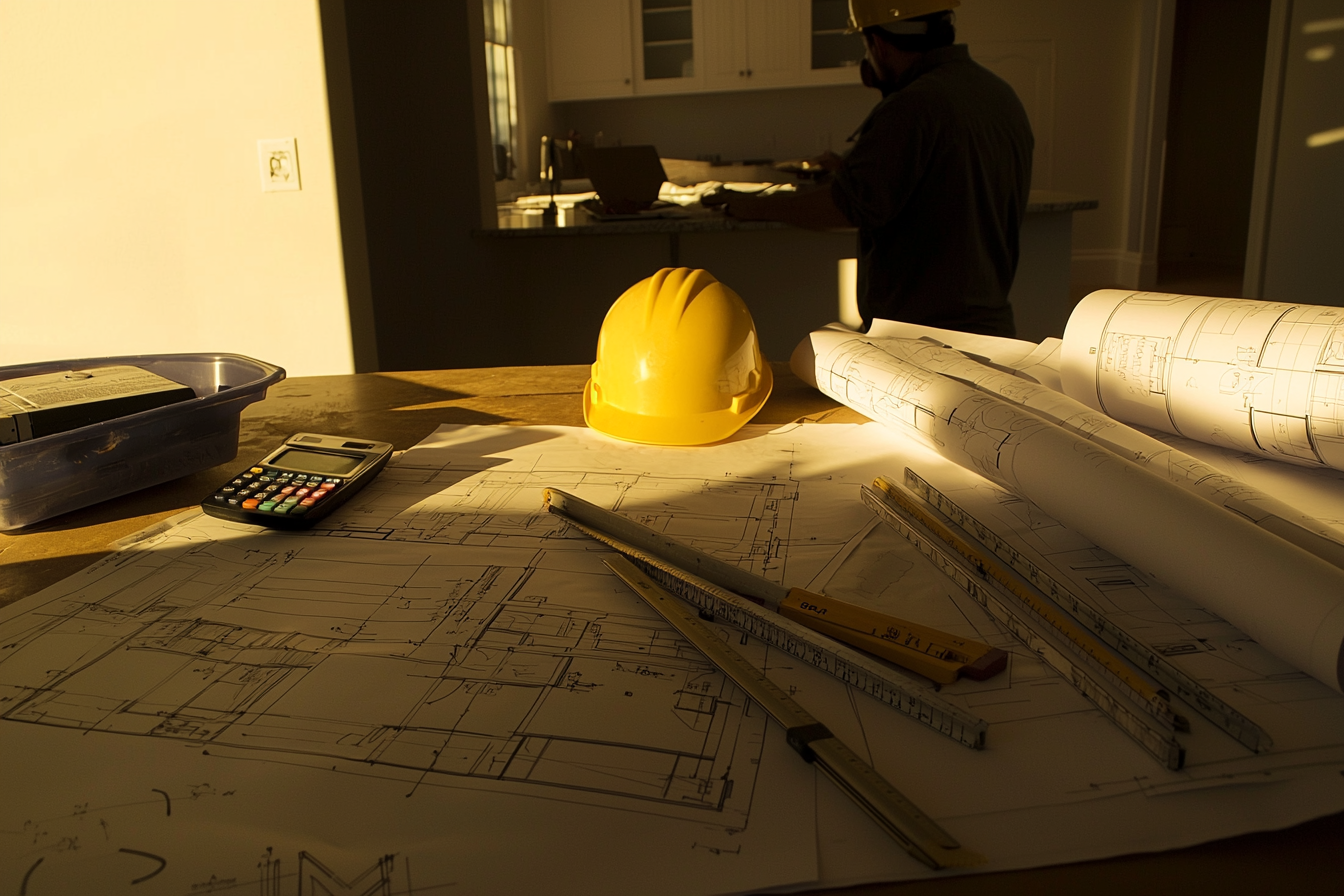
Step-by-Step Process for Conducting a Roofing Takeoff
1. Gather Necessary Information and Documentation
Start by obtaining the architectural plans, blueprints, and site drawings for the project. These documents provide critical details about the roof's layout, dimensions, and design elements. Look for elevation views and cross-sections to understand the roof's shape and structural components. If digital plans are available, use takeoff software to extract measurements directly, reducing manual errors.
Verify the roof type and structural details before proceeding. Different roofing systems—such as flat, gable, or hip roofs—require specific materials and installation methods. Structural elements like trusses, beams, and load-bearing walls affect material needs and installation techniques. Understanding these factors early helps in selecting the right materials and avoiding miscalculations.
Identify any constraints that could impact the takeoff process. Consider factors like roof access, surrounding structures, or local building codes. If the roof includes skylights, chimneys, or mechanical equipment, account for these elements in your material estimates. Some features might require additional flashing, sealants, or reinforcements.
2. Measure Roof Dimensions and Calculate Surface Area
Accurately measuring the roof’s dimensions is important for determining material requirements and ensuring a precise estimate. Start by measuring the roof’s length and width. Multiply these values to get the base surface area, which represents the roof’s footprint without accounting for slope.
Since most roofs are not flat, you need to adjust for slope using a pitch factor. The pitch factor depends on the roof’s rise-to-run ratio and increases with steeper slopes. Apply this factor to the base surface area to calculate the actual surface area, ensuring material estimates align with the roof’s true coverage needs.
3. Assess Roof Slope and Pitch for Accurate Estimation
The slope and pitch of a roof directly affect material calculations. A steeper roof requires more shingles, underlayment, and fasteners compared to a flatter one. If you miscalculate the pitch, you might order too much or too little material, leading to waste or shortages.
To determine the pitch, you can use a pitch gauge, which is a simple tool that attaches to the roof and gives an immediate reading. If you prefer a manual method, you can measure the rise and run of the roof. The rise is the vertical height increase over a 12-inch horizontal distance (run). For example, if the roof rises 6 inches for every 12 inches of run, the pitch is 6:12.
For more precision, use a level and a tape measure. Place the level horizontally against the roof, measure 12 inches along it, and then measure the vertical distance from that point to the roof’s surface. This vertical measurement is the rise, which determines the pitch when expressed as a ratio with the 12-inch run.
Accounting for pitch is necessary when estimating materials like shingles, underlayment, and ridge caps. Manufacturers provide coverage estimates based on a standard pitch, usually around 4:12. If your roof is steeper, those estimates won’t be accurate, and you’ll need to adjust the material calculations accordingly.
4. Identify Special Features and Account for Waste Factors
Special roof features can significantly impact material calculations. Chimneys, vents, skylights, and valleys all require adjustments to ensure you order the right amount of materials. Each of these features alters the layout of roofing materials, often leading to additional cuts and overlaps.
You need to account for waste factors to avoid material shortages or excessive overages. Waste comes from several sources:
- Cutting losses – Trimming shingles or panels to fit around obstacles creates leftover material that might not be reusable.
- Material overlaps – Roofing components, such as underlayment and shingles, have to overlap for proper installation, increasing material requirements.
- Complex roof shapes – Roofs with multiple angles, dormers, or irregular sections require more precise cuts, leading to additional waste.
To improve accuracy, review project blueprints and identify all non-standard roof elements. Then, calculate how much extra material is necessary to accommodate these features. Many contractors apply a standard waste percentage—typically 10–15%—but complex roofs might require adjustments beyond this range.
5. Calculate Material Quantities and Create an Order Plan
Accurately calculating material quantities is important for cost control and efficient project execution. Once you have measured the roof dimensions and accounted for slope, pitch, and waste factors, you have to determine how much of each material is required.
Break down the total roofing surface area into specific material needs:
- Shingles or other roofing materials – Convert the measured roof area into the number of shingles, metal panels, or tiles required, factoring in overlap and waste.
- Underlayment – Calculate the required rolls or sheets based on the roof area and any necessary overlap.
- Flashing – Identify areas where flashing is needed, such as valleys, chimneys, and vents, and measure accordingly.
- Fasteners – Estimate the number of nails or screws based on manufacturer recommendations for the chosen roofing material.
Once you have determined material quantities, develop an order plan that considers supplier availability, delivery timelines, and budget constraints. Check lead times for materials that might have longer wait periods, and schedule deliveries to align with project phases. This helps prevent delays and ensures materials arrive when needed without excessive on-site storage.
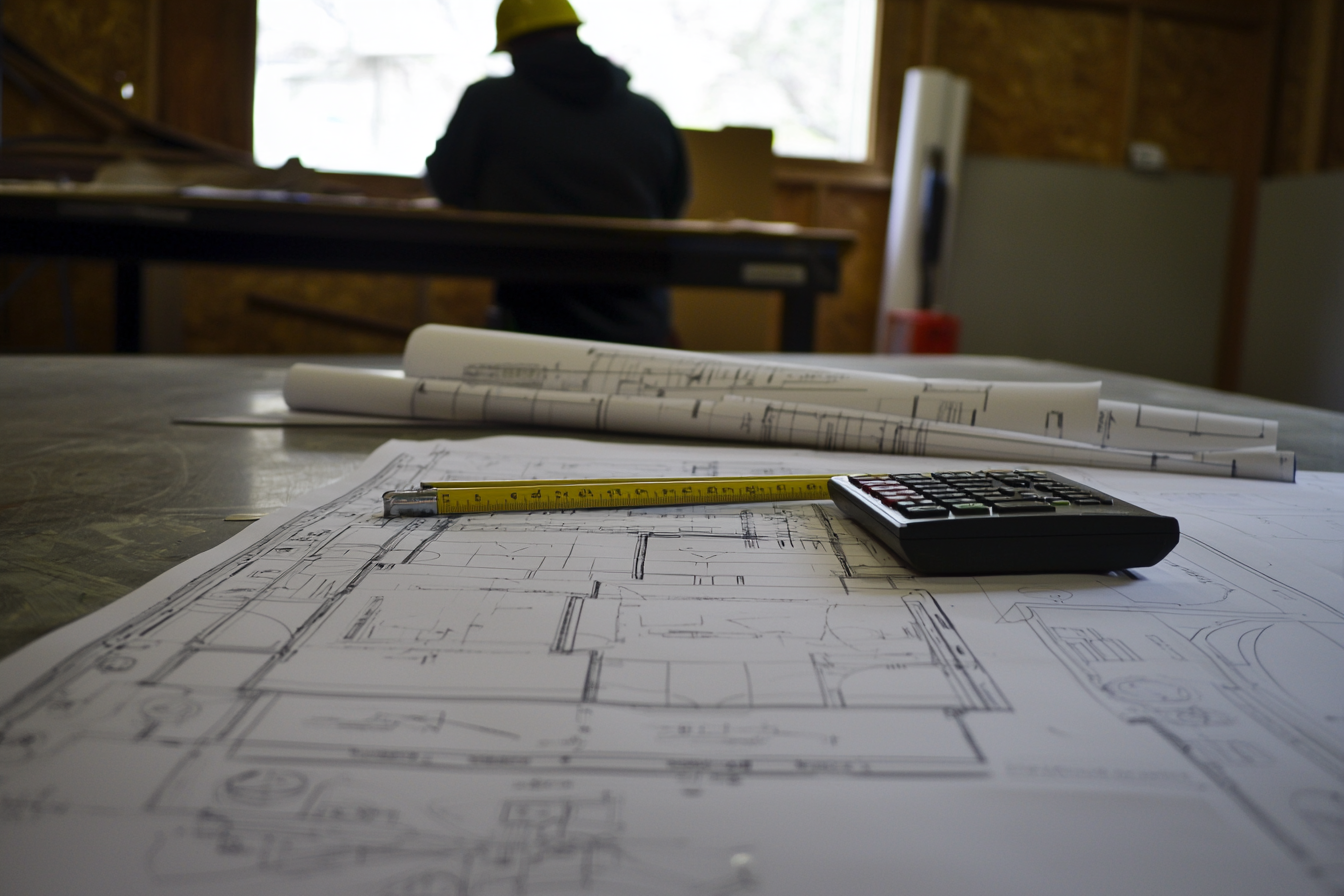
Best Practices for Enhancing Construction Efficiency
1. Update Material Costs and Supplier Data Regularly
Keeping material costs and supplier data updated is important for accurate roofing takeoffs. Prices for roofing materials fluctuate because of supply chain changes, market demand, and seasonal variations. If you rely on outdated cost estimates, your budget can quickly become inaccurate, leading to cost overruns or unexpected expenses.
To prevent pricing discrepancies, regularly update your material cost database. Check with suppliers to confirm current prices for shingles, underlayments, fasteners, and other essential materials. Many suppliers provide price sheets or online catalogs that reflect real-time costs. Reviewing these sources ensures that your estimates align with actual expenses.
Supplier availability also impacts project timelines. If a preferred supplier experiences shortages or delivery delays, you might need to adjust your procurement plan. Keep an updated list of suppliers, including secondary options, to ensure you can source materials when needed. Record key details such as lead times, bulk pricing options, and minimum order requirements.
2. Train Estimators in Roofing Takeoff Techniques
To improve accuracy in roofing takeoffs, estimators need proper training. Small errors in measurements can lead to material shortages or excess waste, both of which increase costs and slow down projects. Learning precise measurement techniques ensures that materials are calculated correctly from the start.
Using digital tools can further improve efficiency. Roofing takeoff software automates calculations, reduces human error, and speeds up the estimating process. Fondion simplifies this process by allowing estimators to measure quantities accurately and generate cost-based quotes automatically. Some programs integrate with supplier databases, providing real-time material costs for more accurate budgeting. Training estimators to use these tools effectively allows for faster and more reliable takeoffs.
Combining hands-on measurement training with digital tool proficiency helps estimators work more efficiently while improving overall project accuracy.
3. Ensure Clear Communication Among Project Stakeholders
Clear communication ensures that everyone involved in a roofing takeoff understands the project requirements and material needs. Miscommunication can cause delays, ordering mistakes, or budget overruns. To prevent these issues, establish structured communication between estimators, contractors, and suppliers.
Use direct channels like emails, project management software, or scheduled meetings to keep everyone aligned. This helps clarify material quantities, delivery schedules, and any project constraints. Standardized documentation, such as material lists and detailed takeoff reports, further reduces misunderstandings. When everyone follows the same reporting format, tracking changes and verifying information becomes easier.
Consistent updates also improve coordination. When material costs change or project conditions shift, quickly sharing this information helps adjust plans without costly errors.
Conclusion
Accurate roofing takeoffs are important for efficient construction planning and cost control. They ensure correct material estimates, reduce waste, and improve project timelines. A well-executed takeoff requires both precision and a structured approach. Investing in proper training, updating material data, and maintaining clear communication can significantly improve accuracy. Consistent improvement in takeoff methods leads to better budgeting and smoother project execution.
Improve Your Roofing Takeoffs with Fondion
Fondion is a construction takeoff and estimating software that helps businesses win more work with faster takeoffs and more accurate estimates. It allows you to measure quantities from a picture and automatically create a quote calculation based on your company's real costs, together with professional tender documents.
By basing calculations on actual costs, Fondion helps you improve profit margins, eliminate costly miscalculations, and create professional proposals effortlessly. It also enhances customer relationships with a CRM designed for construction businesses, ensuring smoother communication and project success.
Start your free Fondion trial today and achieve faster, more precise takeoffs with better profit margins.
FAQ
What Is a Roofing Takeoff?
A roofing takeoff is the process of measuring and estimating the materials needed for a roofing project. It involves calculating the roof’s dimensions, determining required materials, and accounting for waste factors. Accurate takeoffs ensure proper planning, cost control, and efficient material ordering.
Why Is a Roofing Takeoff Important?
A roofing takeoff ensures accurate material estimates, prevents waste, and helps control costs. It improves project planning, minimizes errors, and ensures a smooth workflow. A well-executed takeoff reduces unexpected expenses and delays, leading to better efficiency and profitability. Good construction estimating software creates professional tender documents automatically and with the right content. In that way, you can make sure that you win more projects and have better profit margins because the documents automatically create a detailed list of what is included in the project and what is not included in the project. This way customer satisfaction stays very high while simultaneously you’ll only do the work that you are supposed to do keeping your time schedule and costs on budget.
What Are the Basic Steps Involved in a Roofing Takeoff?
- Measure the roof’s dimensions, including slope and pitch.
- Identify required materials (shingles, underlayment, flashing, etc.).
- Calculate material quantities, factoring in waste.
- Account for special features like skylights and vents.
- Verify calculations to ensure accurate budgeting and procurement.
What Are Some Common Mistakes to Avoid During a Roofing Takeoff?
- Inaccurate measurements lead to shortages or overages.
- Overlooking waste factors and special roof features.
- Ignoring roof pitch and underestimating material needs.
- Misinterpreting blueprints or using outdated plans.
- Not verifying calculations, increases error risks.
What Tools Can Help Me Perform a Roofing Takeoff?
Fondion simplifies roofing takeoffs by providing quick quantity measurements, accurate estimates, and professional proposals based on real costs. It helps reduce miscalculations, improve cost control, and streamline project planning. Make sure that you don’t have to manually enter data into different systems, rather, you can manage all information from a single system. If you are using various systems, the system you choose, like Fondion, should act as the master. This way, you only need to set up projects in one software, which then syncs with other systems. This allows you to accurately estimate and monitor costs while ensuring that you can learn from historical data about your true costs, optimizing your operations for profitability across different areas.