Accurate flooring estimates are essential to control costs and prevent material shortages or excess waste. If measurements are off, even slightly, it can lead to unexpected expenses, project delays, and inefficiencies during installation.
A flooring takeoff is the process of determining the exact quantity of flooring materials required based on project specifications and measurements. It considers factors like floor layout, material waste, and installation requirements to provide a realistic estimate. This article explains the step-by-step process of performing a flooring takeoff for accurate estimations, helping you streamline planning and avoid costly miscalculations.
Learn about material takeoffs by reading "A Comprehensive Guide to Material Takeoffs for Construction Projects."
What is Flooring Takeoff?
Flooring takeoff is the process of determining how much material is needed for a flooring project. It involves measuring the floor area, accounting for material waste, and calculating the total quantity required for installation. Without an accurate takeoff, you risk ordering too little or too much material, leading to delays or unnecessary costs.
In both construction and renovation projects, flooring takeoff plays a critical role in planning and budgeting. Contractors, estimators, and project managers use takeoff data to ensure they order the correct amount of flooring materials, including hardwood, tile, carpet, or vinyl.
This process helps align material quantities with project specifications, preventing costly overruns or shortages.
An effective flooring takeoff contributes to cost efficiency in several ways:
- Prevents material shortages, reducing the risk of project delays.
- Avoids excessive ordering, minimizing waste and unnecessary expenses.
- Improves budgeting accuracy, ensuring that labor and material costs are correctly estimated.
"A flooring takeoff isn’t just a rough estimate—it’s the foundation of a successful project. Even a small miscalculation can throw off your budget or delay installation. The key is to measure carefully, factor in waste, and double-check every number before ordering materials. It’s not about guessing—it’s about getting it right the first time." - - Mika Sievinen, Sales Director at Fondion
Gather Necessary Information and Tools for Flooring Takeoff
To perform a flooring takeoff accurately, you need the right information and tools. Without them, miscalculations can lead to material shortages or excess costs. Gathering the necessary details before starting helps streamline the process and improves estimate reliability.
Start by collecting key project details:
- Floor plans – Ensure you have the most up-to-date drawings. These should include all areas requiring flooring, including closets, hallways, and staircases.
- Project specifications – Review material requirements such as flooring type, thickness, and installation method.
- Material requirements – Identify any underlayment, adhesives, or finishing materials needed for the flooring installation.
Having accurate measurement tools is important for precise takeoff calculations. The tools you need depend on whether you are performing measurements manually or digitally:
- Measuring tape – Useful for small areas and quick verification.
- Laser distance meter – Provides fast and precise room measurements, reducing human error.
- Digital takeoff software – Applications like PlanSwift or Bluebeam Revu allow for efficient area calculations directly from digital blueprints.
To correctly estimate material quantities and costs, you have to have access to up-to-date manufacturer specifications and pricing data. Flooring materials vary in terms of coverage, waste factors, and pricing. Some manufacturers provide coverage rates in square feet per box, while others specify it per plank or tile.
Check for:
- Material coverage rates – This helps determine how many units you need based on the total floor area.
- Waste percentage – Some flooring types, like tile or hardwood, require extra material for cutting and fitting irregular spaces.
- Current pricing – Prices fluctuate based on availability and supplier rates, so always verify costs before finalizing an estimate.
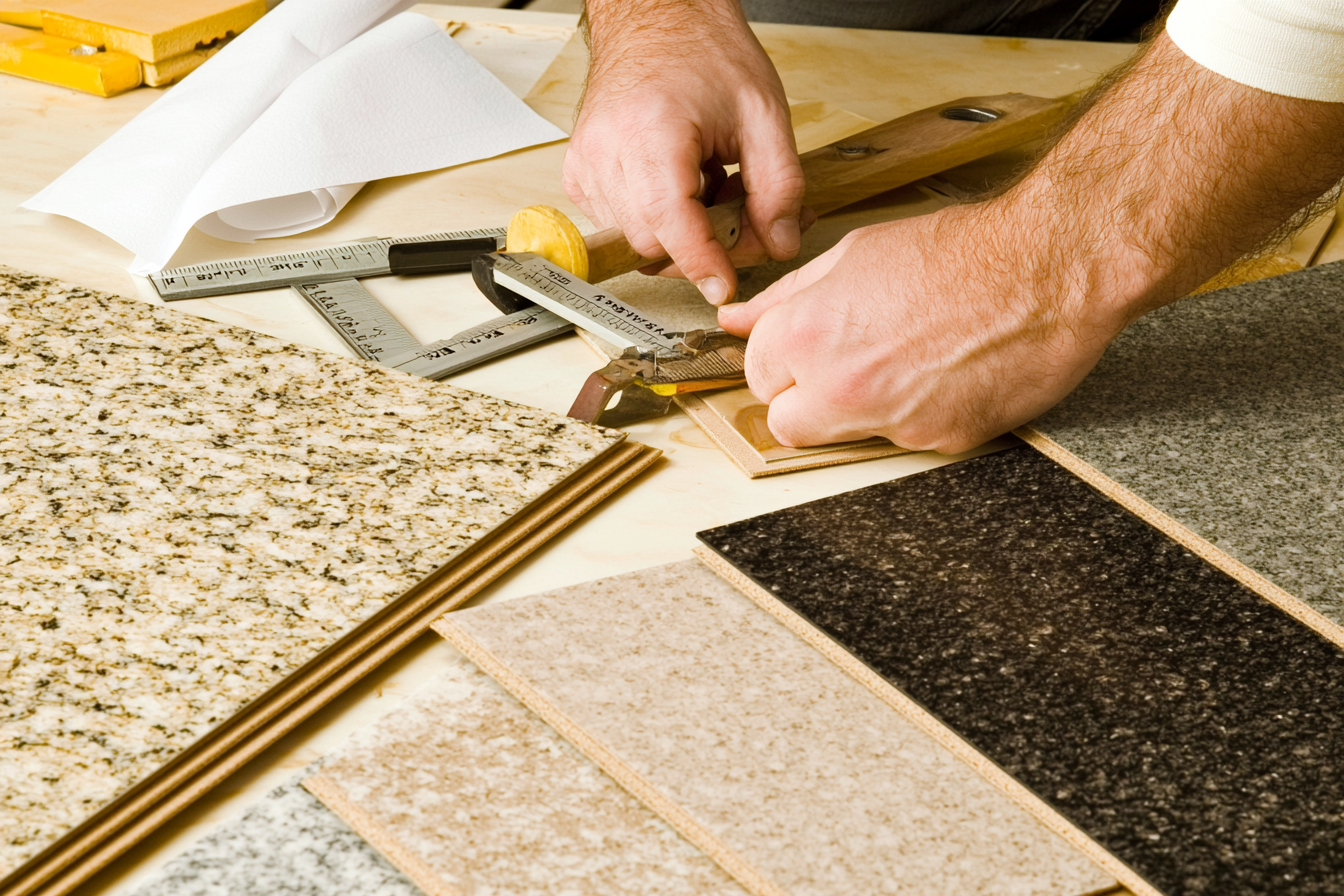
Understand the Flooring Takeoff Process
The process begins with gathering project details, including floor plans, material specifications, and any unique project requirements. Without this information, estimating material needs accurately is impossible.
After this, you have to measure the floor area using a combination of architectural drawings and, if necessary, onsite measurements to verify dimensions. Even small discrepancies in measurements can lead to under or over-ordering materials.
Once measurements are confirmed, the next step is calculating material quantities. This requires factoring in waste percentages, layout patterns, and material-specific considerations. The total flooring material needed is calculated using the formula:
Total Material Needed (sq ft) = Measured Floor Area (sq ft) + Waste Factor (%)
For example, if a project requires 1,000 square feet of flooring and the waste factor is 10%, the total material needed would be 1,100 square feet.
After determining material quantities, you have to estimate costs by incorporating unit prices for flooring materials, adhesives, and other necessary supplies. Additionally, labor costs should be included, considering installation complexity and required workforce hours.
To ensure accuracy, systematically verify all calculations before finalizing the takeoff. A small measurement error or miscalculation in material requirements can lead to budget overruns or delays.
Measure the Floor Area Accurately for Takeoff
Start by identifying the total floor area that requires flooring. Measure each room separately, noting its length and width. For standard rectangular rooms, use the formula:
Floor Area = Length × Width
For irregularly shaped areas, divide them into simpler sections such as rectangles, triangles, or circles. Measure each section separately and calculate its area before adding everything together. If a space includes alcoves, closets, or recesses, ensure they are measured and accounted for in the total area.
When dealing with complex floor plans, break them into manageable sections to reduce measurement errors. Large open areas can be split into grids, with each section measured individually and summed. For L-shaped or T-shaped rooms, treat them as multiple rectangles and add their areas.
Before finalizing the measurements, double-check all dimensions. Small miscalculations can lead to significant discrepancies in material estimates. Verify measurements by comparing them with architectural drawings or by remeasuring critical sections. Using a laser distance meter can improve accuracy, especially in large or irregular spaces.
Once measurements are confirmed, document them clearly. Label each section with its dimensions and total area to streamline the takeoff process.
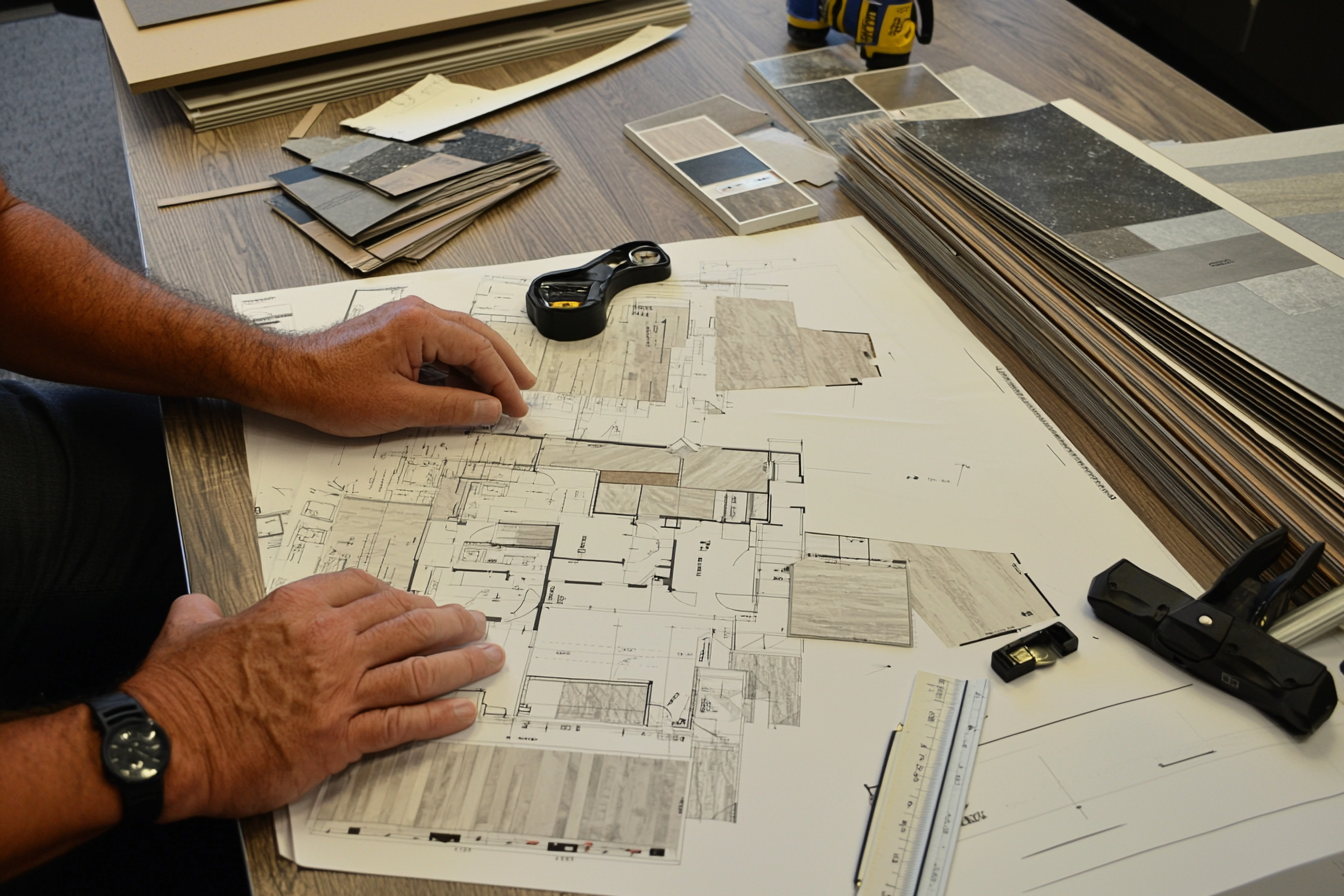
Calculate Flooring Material Quantities for Estimation
Start by determining the total material quantity needed. Use your measured floor area and refer to the material’s specifications, such as coverage per unit. The basic formula for material quantity is:
Material Quantity = Total Floor Area ÷ Coverage per Unit
For example, if you're installing laminate planks that cover 2.5 square feet each and your room is 300 square feet, you’d need:
300 ÷ 2.5 = 120 planks
Next, factor in material waste. Waste occurs because of cutting, fitting, and installation errors. The waste percentage varies based on the flooring type and installation pattern:
- Carpet and vinyl rolls: ~5-10% waste because of trimming and seams
- Hardwood and laminate planks: ~5-15% waste, depending on the pattern (herringbone requires more)
- Tiles: ~10-20% waste, especially for diagonal layouts
To adjust for waste, apply a waste factor:
Adjusted Material Quantity = Material Quantity × (1 + Waste Percentage)
For example, if your tile installation requires 120 tiles and you add a 15% waste factor:
120 × 1.15 = 138 tiles (rounded up)
Different material formats require specific calculations. Rolls (carpet or vinyl) require length and width adjustments, while planks and tiles need unit-based calculations. When using rolls, divide the total floor area by the roll width to determine the required length.
For planks and tiles, check manufacturer recommendations for bundling and packaging to avoid ordering incomplete sets.
Estimate Material, Labor, and Total Flooring Cost
Accurate cost estimation ensures that flooring projects stay within budget. To achieve this, you need to calculate material costs, estimate labor expenses, and account for additional costs that impact the total estimate.
To determine material costs, multiply the required flooring quantities by the current market price per unit. Prices vary based on flooring type, supplier, and location, so always check with multiple vendors to get accurate figures.
If your project requires different flooring materials, break down the costs separately for each type. Also, factor in waste percentage, which depends on the flooring pattern and cutting requirements. A typical waste factor is 5%–10%, but complex designs might require more.
Labor costs depend on installation complexity, labor rates, and project duration. If the flooring type requires specialized skills, expect higher labor costs. Calculate labor expenses using this formula:
Labor Cost = (Hourly Rate × Number of Workers) × Estimated Hours
For larger projects, pay structure matters. Some contractors charge per square foot, while others charge based on time. Research local rates and past project timelines to make realistic estimates.
Beyond materials and labor, include other expenses that affect the final cost:
- Underlayment and adhesives – Required for certain flooring types like vinyl, laminate, and tile.
- Delivery fees – vary based on supplier policies and distance.
- Subfloor preparation – Additional leveling or moisture barriers might be necessary.
- Permits and disposal costs – Some projects require permits, and old flooring removal adds disposal fees.
Compare Manual vs. Digital Flooring Takeoff Methods
Accuracy differs significantly between the two methods. Manual takeoff relies on physical measurements and printed plans, which can introduce human errors from misreading dimensions or miscalculating quantities. Digital takeoff, on the other hand, reduces these risks by using calibrated digital drawings. However, accuracy in digital methods depends on correctly setting the scale and ensuring software calibration.
Efficiency is another key difference. Manual takeoff is time-consuming, requiring hand calculations and repeated measurements. In contrast, digital takeoff speeds up the process by automating calculations and allowing users to copy and apply measurements across multiple areas. Features like Search in digital tools can quickly count repeating elements, such as tiles or planks, across multiple drawings. A user once used this feature to count 2,870 items in just 2.5 minutes, a task that would take hours manually.
Cost considerations play a major role in selecting a method. Manual takeoff requires minimal upfront investment—just a scale ruler, calculator, and printed plans. However, the labor time involved can lead to higher long-term costs. Digital takeoff software requires an initial investment, with tools like Fondion offering advanced features for streamlining takeoff processes. Some software solutions include dynamic linking to Excel, enabling real-time cost updates based on material quantities and unit prices. While the software cost might seem high, the time saved often offsets the expense.
For small projects with simple layouts, manual takeoff can be sufficient. However, for large-scale or complex projects, digital takeoff provides greater accuracy, efficiency, and long-term cost savings. Fondion helps construction businesses improve their estimating process by enabling quick quantity takeoffs, ensuring estimates are based on actual company costs, and generating professional proposals that enhance project success.
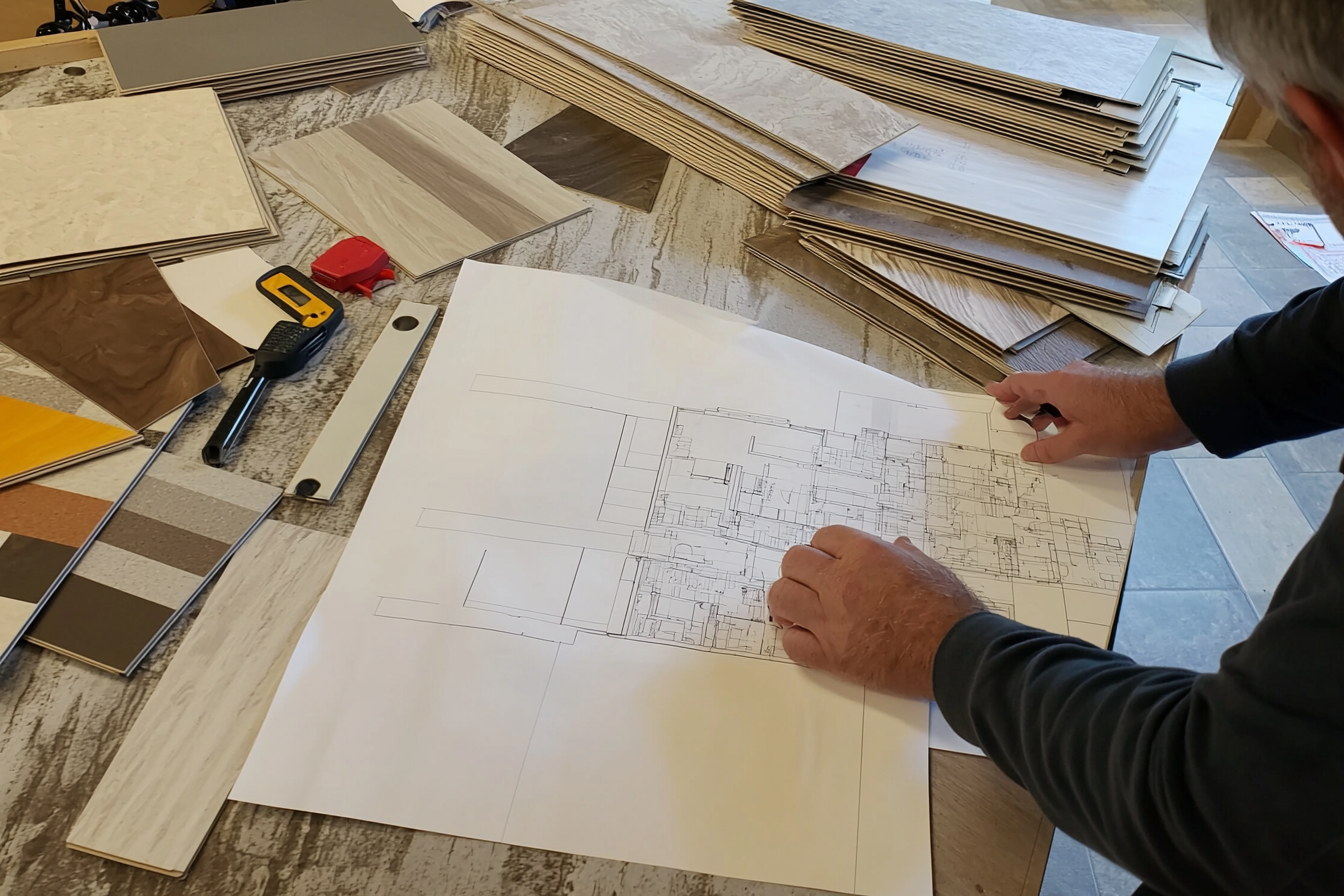
Review and Finalize the Flooring Takeoff Estimate
Start by cross-checking all measurements and calculations. Compare the area measurements with the original plans to confirm accuracy. If you used manual measurements, verify them against digital tools or previous records. Check that all floor sections, including irregular areas and cutouts, are accounted for.
Next, factor in material waste and variations. Flooring materials often require extra stock because of cutting, pattern matching, and installation losses. Common waste factors include:
- 5-10% extra for standard installations.
- 10-15% extra for diagonal or complex layouts.
- 15-20% extra for materials with significant pattern alignment needs.
Adjust your final material quantities accordingly to avoid shortages while minimizing excess.
After verifying quantities, review cost estimates for materials, labor, and additional expenses. Ensure that:
- Unit prices for flooring materials match supplier quotes.
- Labor rates align with the project's scope and complexity.
- Additional costs, such as adhesives, underlayment, and delivery fees, are included.
For accuracy, use cost formulas where applicable. For example, if labor costs $3 per square foot and the project covers 1,200 square feet:
Labor cost = 1,200 sq. ft. × $3/sq. ft. = $3,600
Finally, double-check for inconsistencies. Compare your final estimate with past projects of similar scale. If discrepancies arise, revisit your calculations before finalizing. A second review by another estimator or team member can also help catch errors.
Follow Best Practices and Avoid Mistakes in Flooring Takeoff
Ensuring an accurate flooring takeoff requires a systematic approach. Skipping steps or working without a clear process increases the risk of miscalculations. Follow a structured method from start to finish, consistently applying the same approach across all projects. This not only improves accuracy but also makes it easier to review and verify numbers.
Several common mistakes can lead to inaccurate estimates:
- Overlooking irregular floor shapes – Rooms with alcoves, columns, or curved walls require additional attention. Break these areas into smaller, measurable sections instead of estimating them as standard rectangles.
- Failing to account for waste factors – Flooring materials often require extra because of cutting and fitting. The waste percentage varies by material type, with carpet and vinyl typically needing 5-10% extra, while tile might require 10-15%.
- Misinterpreting project specifications – Always review material requirements, installation methods, and subfloor conditions. A mismatch between specified and estimated materials can lead to cost overruns or project delays.
Regular verification and cross-checking of measurements and quantities prevent errors from compounding. Compare your figures against prior estimates, architectural plans, and supplier data. If using digital takeoff tools, ensure scaling is correctly calibrated before taking measurements.
Even small miscalculations can result in significant cost differences. A project that underestimates flooring by 10% might require emergency material purchases, leading to higher costs and delays. Fondion helps construction professionals avoid these issues by enabling quick quantity takeoffs, generating precise estimates based on real company costs, and automating professional proposals. With Fondion, you can streamline the takeoff process and make more informed financial decisions.
Conclusion
Accurate flooring takeoff ensures reliable cost estimates and prevents budget overruns. It's both a technical process and a critical planning step that affects project efficiency. Using the right tools, verifying measurements, and following best practices improve accuracy. A well-executed takeoff saves time, reduces waste, and leads to better project outcomes.
Perform Flooring Takeoff More Accurately with Fondion
Fondion is a construction takeoff and estimating software designed to help businesses perform flooring takeoffs with greater speed and precision. It allows you to measure quantities directly from images, automate cost calculations based on real company expenses, and generate professional proposals in minutes.
With Fondion, you can improve profit margins, speed up the estimating process, and provide clear, well-structured project proposals that win more work. Start your free Fondion trial today and take the guesswork out of your flooring takeoff process!
FAQ
What Is a Flooring Takeoff?
A flooring takeoff is the process of measuring and estimating the materials needed for a flooring project. It calculates total square footage, accounts for waste, and determines material requirements. Accurate takeoffs help avoid shortages, reduce excess costs, and ensure precise budgeting.
What Is the Best Flooring Takeoff Software?
The best flooring takeoff software depends on project needs. Look for features like digital takeoff, cost estimation, and reporting to improve accuracy and efficiency. Fondion helps streamline quantity takeoffs, generate precise estimates based on real company costs, and create professional proposals. Good construction estimating software creates professional tender documents automatically and with the right content. In that way, you can make sure that you win more projects and have better profit margins because the documents automatically create a detailed list of what is included in the project and what is not included in the project. This way customer satisfaction stays very high while simultaneously you’ll only do the work that you are supposed to do keeping your time schedule and costs on budget.
What Is the Rule of 3 Flooring?
The Rule of 3 means measuring length, and width, and adding a waste factor (5-10%) to ensure accurate flooring estimates. This method accounts for cutting waste, pattern alignment, and installation errors, preventing material shortages or excess costs.
Do Flooring Companies Remove Old Flooring?
Yes, most flooring companies offer removal services, but costs vary. Some include it in the total price, while others charge extra based on material and labor. Always confirm with your contractor and factor removal costs into your estimate.
How Do I Account for Waste and Transitions in My Flooring Takeoff?
Include a waste percentage based on material type—5-10% for standard layouts, up to 15% for complex ones. Factor in room shapes, pattern alignment, and extra material for mistakes or repairs. For transitions, measure and include threshold materials to ensure full coverage. Make sure that you don’t have to manually enter data into different systems, but rather, you can manage all information from a single system. If you are using various systems, the system you choose, like Fondion, should act as the master. This way, you only need to set up projects in one software, which then syncs with other systems. This allows you to accurately estimate and monitor costs while ensuring that you can learn from historical data about your true costs, optimizing your operations for profitability across different areas.