Contractors and project managers often struggle with estimating the materials needed for heating, ventilation, and air conditioning (HVAC) systems accurately and end up facing material shortages, budget overruns, or costly delays. HVAC takeoff is the process of determining the exact quantity of ductwork, piping, fittings, and equipment required for a project, ensuring smooth procurement and installation.
This article explains what HVAC takeoff is, why it is essential in construction, and how to perform it step by step. You’ll also learn about key components, best practices, and tools that streamline the process.
Find out more about material takeoffs in "A Comprehensive Guide to Material Takeoffs for Construction Projects."
Purpose of HVAC Takeoff in Construction
HVAC takeoff is the process of quantifying materials needed to install an HVAC system in a construction project. Unlike general material takeoff, which covers all building materials, HVAC takeoff focuses specifically on components such as ductwork, piping, and equipment.
This process ensures that the right materials are available in the correct quantities, preventing shortages or excess materials that could lead to waste.
Accurate HVAC takeoff plays an essential role in cost planning. By determining material quantities in advance, contractors and project managers can allocate budgets efficiently, ensuring that costs align with project estimates.
Without precise takeoff data, unexpected expenses can arise from last-minute material orders, incorrect equipment sizing, or miscalculations in labor costs. A well-executed takeoff provides a clear financial roadmap, reducing the risk of budget overruns.
In addition to cost control, HVAC takeoff helps minimize material waste and prevent installation errors. Ordering excess materials increases expenses and storage challenges, while underordering can delay construction.
By quantifying components accurately, HVAC takeoff ensures that procurement teams purchase only what is necessary. This accuracy also supports smooth installation, as technicians receive the correct materials and specifications, reducing the likelihood of rework or adjustments on-site.
"If your HVAC takeoff isn't accurate, you're setting yourself up for trouble before the job even starts. Too much material? That's wasted money. Too little? You're delaying the project. A solid takeoff isn't just about counting parts—it's about making sure everything fits the design, the budget, and the schedule. Get it right, and the rest of the job runs a lot smoother." - - Ari Aarniovuori, Deployment & Support at Fondion
Key Components of HVAC Systems in Takeoff
The most important components in an HVAC takeoff include:
- Ductwork – Ducts distribute conditioned air throughout the building. Takeoff involves measuring lengths, widths, and diameters, depending on the duct type. Rectangular, round, spiral, and flexible ducts have to be accounted for separately based on their specifications.
- Piping – Pipes transport refrigerant, chilled water, or heating fluids. The takeoff has to include pipe diameters, lengths, and insulation requirements to ensure proper system function and energy efficiency.
- Fittings – Elbows, tees, reducers, and transitions connect ducts and pipes, allowing airflow and fluid movement. Each fitting type affects pressure loss and overall system efficiency, making accurate quantification essential.
- HVAC Equipment – Air handling units, rooftop units, chillers, boilers, and heat pumps have to be selected based on load calculations and building requirements. Their capacity, power requirements, and placement impact overall system design.
- Accessories – Registers, grilles, diffusers, dampers, and hangers contribute to airflow control and system stability. The takeoff has to consider their sizes, quantities, and placement in relation to the duct and piping layout.
- Insulation – Duct and pipe insulation reduces heat loss, prevents condensation, and improves system efficiency. Different insulation materials and thicknesses are required based on project specifications.
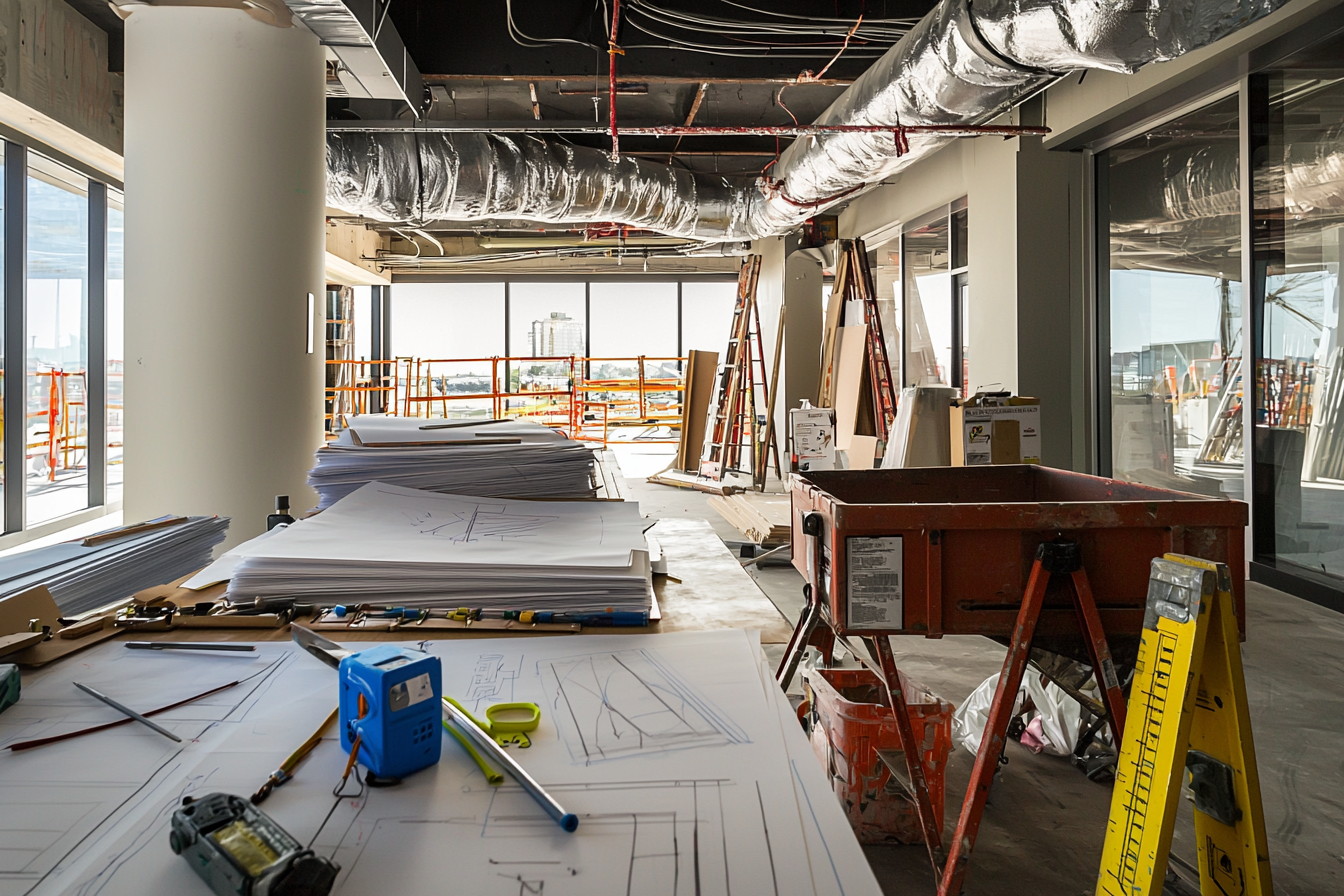
Steps Involved in the HVAC Takeoff Process
1. Review project plans and specifications
Before starting an HVAC takeoff, you need to analyze the architectural and mechanical drawings of the project. These documents define the layout and constraints that impact HVAC system design. Without a thorough review, you risk misjudging material requirements, leading to cost overruns or installation issues.
Architectural drawings provide key details such as:
- Building layout – The size and shape of rooms affect airflow and duct placement.
- Ceiling heights – These influence duct routing and equipment clearance.
- Wall and floor penetrations – Openings for ducts and pipes have to align with structural elements.
Mechanical drawings focus on HVAC-specific details, showing:
- Duct and piping routes – These indicate how air and fluids will move through the building.
- Equipment locations – The placement of air handlers, condensers, and fans affects system efficiency.
- Airflow requirements – Specifications on ventilation rates help size ducts properly.
By reviewing these documents, you ensure that your HVAC takeoff aligns with the project’s design and performance requirements. This step helps prevent material shortages, installation conflicts, and compliance issues later in construction.
2. Measure building dimensions
Measuring building dimensions is important for determining HVAC system requirements and material quantities. The size and shape of a building directly affect airflow, temperature control, and equipment capacity.
Several key dimensions have to be measured carefully:
- Floor area – Determines the total space that needs heating or cooling, influencing system capacity and ductwork layout.
- Ceiling height – Affects air distribution and heat load calculations, as taller spaces require different airflow considerations.
- Room volume – Helps calculate the total air exchange needed for proper ventilation, ensuring comfort and indoor air quality.
These measurements guide HVAC system design, helping to select the right equipment and estimate materials such as ductwork, piping, and insulation.
3. Calculate heating and cooling loads
Heating and cooling load calculations determine the HVAC system's required capacity. These calculations ensure the system can maintain comfortable indoor conditions without being oversized or undersized.
An oversized unit cycles on and off frequently, reducing efficiency and lifespan. An undersized unit struggles to meet demand, leading to excessive wear and poor climate control.
Load calculations consider multiple factors, including:
- Building size and layout – Larger spaces require more heating and cooling capacity.
- Insulation levels – Better insulation reduces heat loss in winter and heat gain in summer.
- Window size and orientation – Windows affect solar heat gain and heat loss.
- Occupancy levels – More occupants generate more heat, increasing cooling needs.
- Internal heat sources – Appliances, lighting, and equipment contribute to the heat load.
- Climate conditions – Outdoor temperatures and humidity influence system demand.
4. Select appropriate HVAC equipment
Selecting the right HVAC equipment is important to ensure system efficiency and compliance with project specifications. Equipment that does not match the building's heating and cooling load requirements can lead to inefficiencies, higher energy costs, and potential system failures.
To make the right selection, you need to consider several factors:
- Heating and cooling loads – The equipment has to be sized to match the calculated load to provide adequate temperature control without excessive energy use.
- System compatibility – The selected units should integrate seamlessly with ductwork, piping, and other HVAC components.
- Energy efficiency ratings – Choosing high-efficiency units can reduce operating costs and improve long-term performance.
- Regulatory compliance – The equipment has to meet local building codes and industry standards for safety and efficiency.
- Project constraints – Space limitations, noise levels, and maintenance access should all influence equipment selection.
5. Design ductwork and piping layouts
Planning ductwork and piping layouts is important for ensuring proper airflow, energy efficiency, and compliance with space constraints. A well-designed layout reduces pressure losses, minimizes noise, and optimizes air distribution throughout the building.
To create an efficient layout, consider the following factors:
- Space availability – Ensure ductwork and piping fit within the allocated ceiling, wall, or floor spaces without interfering with other building systems.
- Airflow efficiency – Minimize sharp turns and excessive duct length to reduce resistance and improve system performance.
- Load distribution – Balance airflow across different zones by adjusting duct and pipe sizing according to calculated heating and cooling loads.
- Accessibility for maintenance – Design layouts that allow easy access to key components like dampers, filters, and valves for servicing.
Duct sizing is another key step. Undersized ducts increase resistance and energy consumption, while oversized ducts lead to unnecessary material costs. Static pressure calculations help determine the right duct dimensions to maintain adequate airflow.
Piping layouts have to support efficient refrigerant or hydronic flow. Pipe routing should avoid unnecessary bends, which can cause pressure drops and reduce system efficiency. Proper insulation also prevents heat loss and condensation issues.
6. Quantify materials and components
To determine the required quantities, you have to analyze project specifications and system design. This involves reviewing architectural and mechanical plans to identify all necessary HVAC components. Key materials that have to be quantified include:
- Ductwork – Measure lengths, widths, and diameters for both rectangular and round ducts.
- Piping – Calculate the total length and required diameters for refrigerant, condensate, and hydronic piping.
- Fittings and connectors – Include elbows, tees, reducers, and transitions needed for proper airflow and fluid movement.
- Insulation – Determine the amount required for ductwork and piping to improve efficiency and prevent condensation issues.
- HVAC equipment – Account for air handling units, furnaces, chillers, and condensers based on system capacity.
- Accessories – Quantity grilles, registers, diffusers, dampers, and hangers to ensure proper air distribution and support.
Each component has to align with the project's engineering requirements and code compliance. Overestimating results in unnecessary costs, while underestimating can lead to shortages and project delays.
7. Compile a bill of materials
To ensure accurate budgeting and procurement, you have to compile a comprehensive bill of materials (BOM) for the HVAC system. This document lists every component required for the installation, preventing shortages or unexpected costs during construction.
A complete BOM should include:
- Ductwork – Rectangular, round, or spiral ducts with specified dimensions.
- Fittings and accessories – Elbows, tees, reducers, dampers, and hangers.
- HVAC equipment – Air handling units, furnaces, chillers, heat pumps, and condensers.
- Piping and insulation – Copper or PEX pipes, along with insulation for thermal efficiency.
- Registers, grilles, and diffusers – Air distribution components sized for airflow requirements.
- Fasteners and supports – Screws, brackets, and hangers for structural stability.
Each item should include details such as quantity, size, material type, and specifications to match project requirements. By organizing the BOM properly, you can streamline purchasing, reduce waste, and ensure the HVAC system is installed without delays.
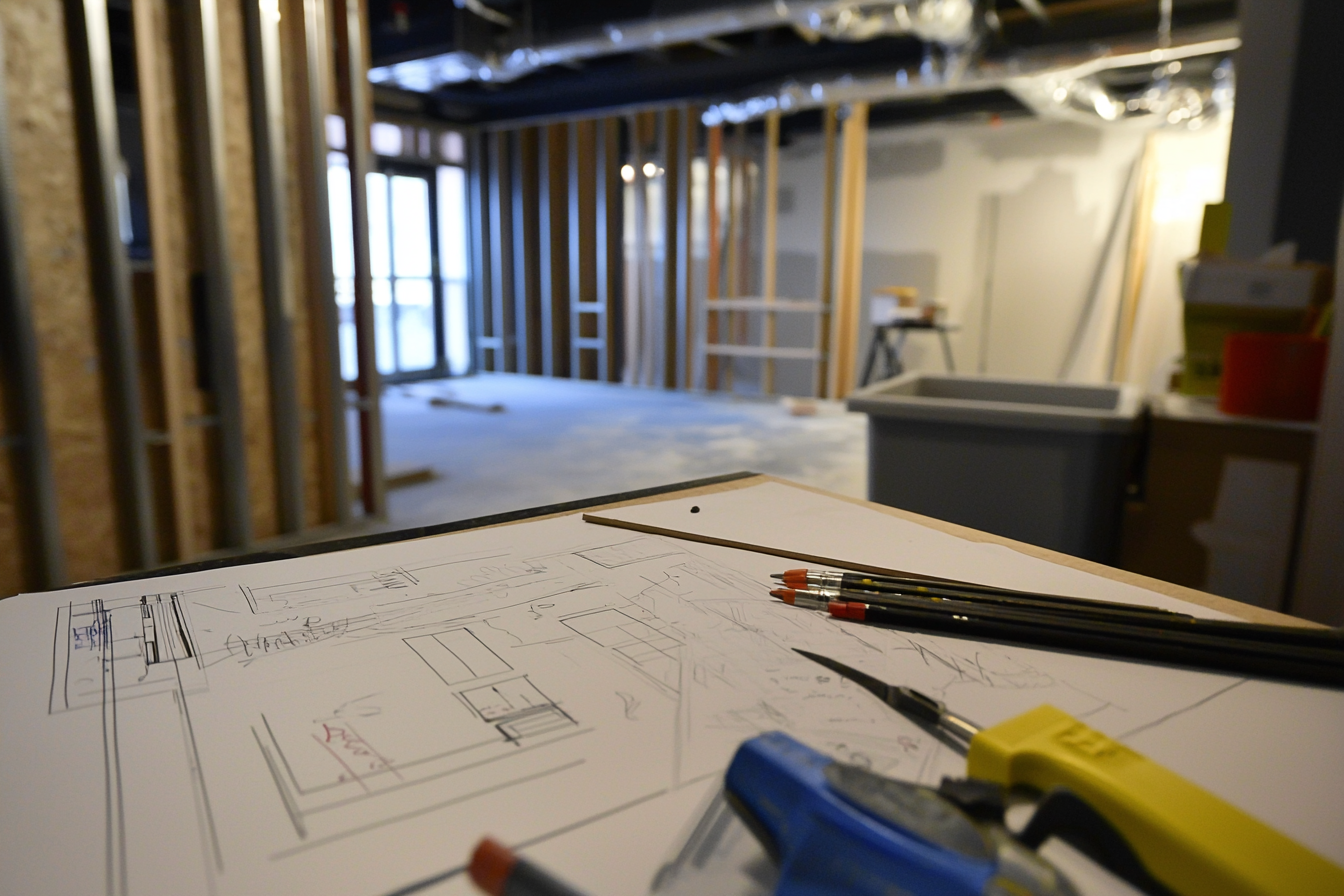
"Manual takeoffs can be time-consuming and prone to errors. If you miss a single component or miscalculate material quantities, it can throw off your entire budget and schedule. That’s why using the right software isn’t just a convenience—it’s a necessity for accurate, efficient estimating." - - Jukka-Pekka Tahkola, Managing Director at Fondion
Tools and Software for HVAC Takeoff
Specialized HVAC takeoff software improves accuracy and efficiency by automating calculations and reducing manual errors. Instead of relying on traditional manual methods, digital tools streamline the process by extracting material quantities directly from project drawings. This minimizes miscalculations, ensures consistency, and saves time.
Several tools are commonly used for HVAC takeoff, including:
- Digital takeoff applications – These tools allow estimators to measure and quantify HVAC components directly from digital blueprints, improving speed and accuracy.
- BIM-integrated solutions – Building Information Modeling (BIM) software enables real-time collaboration and precise material takeoffs by integrating HVAC design with project planning.
- AI-powered automation tools – Some platforms utilize artificial intelligence to automate HVAC takeoff with high accuracy, reducing manual input.
Among these solutions, Fondion stands out as an advanced takeoff and estimating software tailored for construction professionals. Fondion helps contractors speed up takeoffs, improve cost estimation, and generate professional proposals effortlessly. By basing calculations on real company costs, it enhances profitability and eliminates guesswork.
Additionally, Fondion includes a built-in CRM system to improve communication with clients and ensure smoother project coordination.
With the right construction takeoff and estimation software like Fondion, contractors can work faster, reduce material waste, and improve overall project efficiency.
Applications of HVAC Takeoff in Construction
During the planning phase, HVAC takeoff helps you estimate the exact materials, costs, and labor required for the project. This step is important for creating a realistic budget and preventing cost overruns.
Without a precise takeoff, you might underestimate the materials needed, leading to shortages, or overestimating them, increasing waste and unnecessary expenses.
Once planning is complete, takeoff data becomes important for procurement. Ordering the right quantities of ductwork, piping, and HVAC equipment ensures that materials arrive on time, preventing construction delays.
It also reduces excess inventory, which can take up storage space and increase costs. By aligning procurement with takeoff data, you can avoid last-minute rush orders and unexpected shortages.
During installation and execution, HVAC takeoff ensures smooth coordination between teams. Contractors rely on accurate material lists and layouts to install ductwork, piping, and equipment according to project specifications.
Proper takeoff data helps avoid miscalculations that could lead to inefficient system performance or costly rework. It also ensures compliance with design plans, preventing conflicts with other building systems.
By integrating HVAC takeoff into every stage of construction, you improve efficiency, reduce costs, and ensure the project stays on track.
Conclusion
HVAC takeoff is both a planning tool and a cost-management strategy. It ensures accurate material estimates, reducing waste and preventing budget overruns. As projects grow in complexity, using specialized tools and organized workflows becomes important for efficiency.
A precise takeoff process improves coordination, keeps projects on track, and supports better decision-making. Investing time in accuracy early on leads to smoother execution and fewer delays.
Fondion – Faster & More Accurate HVAC Takeoffs
Fondion is a construction takeoff and estimating software that helps contractors complete faster and more accurate HVAC takeoffs. By automating quantity calculations and ensuring estimates are based on real company costs, Fondion improves profitability and reduces costly errors.
With Fondion, you can:
- Perform quick and precise HVAC takeoffs to streamline project planning.
- Base estimates on actual costs, improving budgeting accuracy.
- Generate professional proposals automatically, saving time.
- Enhance client communication with an integrated CRM for better coordination.
Start your free Fondion trial today and optimize your HVAC takeoff process!
FAQ
What Is a Takeoff in HVAC?
An HVAC takeoff is the process of measuring and estimating materials, ductwork, and equipment needed for an HVAC system. It ensures accurate budgeting, reduces waste, and helps with efficient installation.
How Much Does It Cost To Have an HVAC Guy Come Out?
The cost varies based on location and job complexity. A diagnostic visit typically costs $75–$200, with repairs or additional work increasing the total. Emergency calls may have higher fees.
What Is the Rule For Duct Takeoff?
Duct takeoffs should be placed at least 12 inches from fittings and ideally at a 45-degree angle for smooth airflow. Proper sizing, sealing, and insulation help maintain efficiency and prevent energy loss.
Is HVAC a Write-Off?
HVAC takeoff and write-off are different. A takeoff estimates materials for installation, while a write-off refers to tax deductions for HVAC expenses. Tax eligibility depends on specific regulations. Make sure that you don’t have to manually enter data into different systems, rather, you can manage all information from a single system. If you are using various systems, the system you choose, like Fondion, should act as the master. This way, you only need to set up projects in one software, which then syncs with other systems. This allows you to accurately estimate and monitor costs while ensuring that you can learn from historical data about your true costs, optimizing your operations for profitability across different areas.
What Are the Different Methods For Performing an HVAC Takeoff?
HVAC takeoffs can be done manually, digitally, or with automated software. Manual methods involve blueprint analysis, while digital and automated tools improve accuracy and efficiency. The best approach depends on project size and budget. Good construction estimating software creates professional tender documents automatically and with the right content. In that way, you can make sure that you win more projects and have better profit margins because the documents automatically create a detailed list of what is included in the project and what is not included in the project. This way customer satisfaction stays very high while simultaneously you’ll only do the work that you are supposed to do keeping your time schedule and costs on budget.