Accurate earthwork takeoffs are key to keeping construction projects on budget and schedule. Underestimating can lead to delays and extra costs while overestimating can waste resources. Small mistakes in volume calculations, material estimates, or site conditions can cause big problems later, affecting project timelines and profitability.
Modern construction relies on precise takeoff data to plan excavation, backfilling, and grading efficiently. Using the right estimation methods and tools ensures better resource allocation, minimizes rework and helps avoid costly surprises during execution. This article covers essential tips to improve accuracy when performing an earthwork takeoff, helping you streamline operations and enhance project success.
Get detailed insights on material takeoffs in "A Comprehensive Guide to Material Takeoffs for Construction Projects."
What is Earthwork Takeoff?
Earthwork takeoff is the process of calculating how much soil, rock, or other material needs to be excavated or filled at a construction site. This step is important for preparing accurate project estimates and ensuring that enough material is available without unnecessary waste.
In construction, earthwork takeoff plays a key role in several areas:
- Material Estimation – Knowing the exact volume of material to be moved helps prevent shortages and excesses, keeping costs under control.
- Cost Projections – Accurate takeoff calculations allow for precise budgeting, reducing the risk of unexpected expenses during the project.
- Resource Planning – With proper takeoff data, contractors can schedule labor, equipment, and materials efficiently, avoiding delays and unnecessary costs.
Without precise earthwork takeoff, projects risk running over budget, facing material shortages, or encountering scheduling conflicts. By ensuring accurate calculations, construction teams can improve efficiency and minimize financial risks.
"In earthwork, even a small miscalculation can throw off your entire project. If your takeoff is off by just a few percent, you’re either running out of material mid-job or paying for what you don’t need. The key is precision—use accurate site data, factor in shrink and swell, and always double-check your numbers. That’s how you keep your project on track and your budget in check." - - Marko Valli, Chairman of the Board at Fondion
Importance of Earthwork Takeoff in Construction Projects
Accurate earthwork takeoff determines the volume of soil that has to be excavated, moved, or filled, directly affecting material costs, equipment needs, and labor expenses. Underestimating quantities can lead to unexpected costs while overestimating can result in wasted materials and inflated budgets. A precise takeoff ensures financial feasibility by aligning estimates with actual project requirements.
Scheduling also relies heavily on earthwork takeoff. Excavation and grading are often among the first steps in a project, and delays at this stage can disrupt the entire construction timeline. An accurate estimation helps allocate time and resources efficiently, ensuring that equipment and crews are scheduled appropriately. This minimizes downtime and prevents costly delays caused by miscalculations in earthwork quantities.
Beyond budgeting and scheduling, earthwork takeoff contributes to overall project success in several ways:
- Reduces material waste – Accurate calculations prevent excess soil movement and unnecessary hauling costs.
- Improves workflow coordination – Contractors can plan excavation, grading, and compaction activities more effectively, avoiding conflicts between different trades.
- Minimizes unexpected site issues – A well-prepared takeoff identifies potential challenges, such as unsuitable soil conditions or drainage concerns, before work begins.
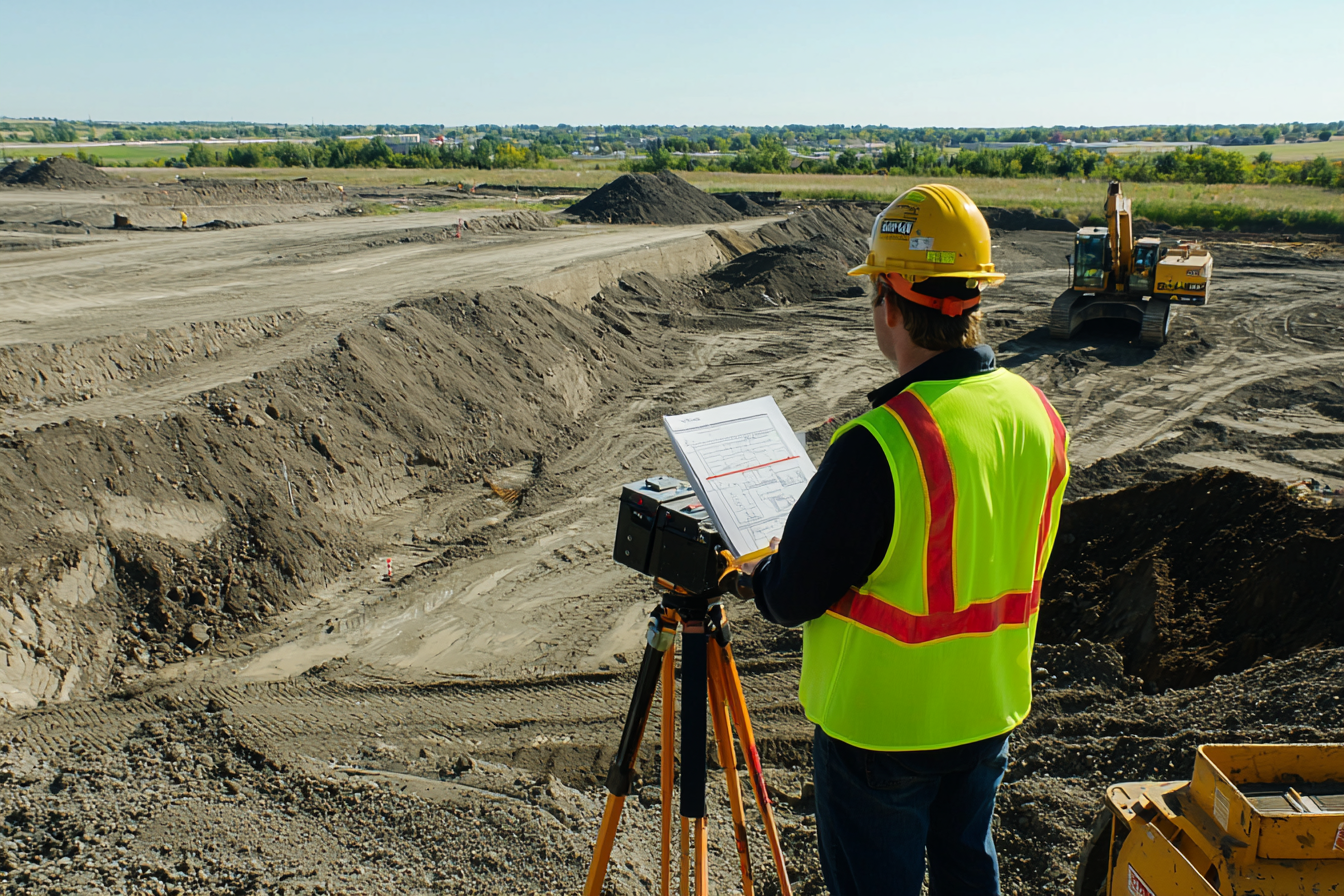
Key Components of Earthwork Takeoff
The first critical component is gathering accurate data. Several sources provide essential information for earthwork takeoff, including:
- Topographic surveys – These show existing ground elevations and help determine how much material needs to be moved.
- Site plans – These outline design elevations, grading requirements, and boundaries for the project.
- Geotechnical reports – These provide soil composition data, which influences excavation, compaction, and fill requirements.
Using these data sources ensures that takeoff calculations are based on real-site conditions instead of assumptions.
Another essential element is selecting the right volume calculation method. Earthwork takeoff requires determining how much material has to be excavated or filled to match design specifications. The two main calculations involved are:
- Cut calculations – Measuring the amount of material that needs to be removed.
- Fill calculations – Determining the volume of material required to bring an area to the desired elevation.
Different methods, such as the average end-area, grid-cell, or cross-section approach, help estimate these quantities with varying levels of accuracy. Choosing the right method depends on the project's complexity and available data.
Adjusting for compaction and shrinkage is also important. When soil is excavated, it expands, and when placed as fill, it compresses. Without accounting for these factors, material shortages or surpluses can occur. Two key adjustments include:
- Shrinkage factor – Soil volume decreases when compacted, requiring more material than initially estimated.
- Swell factor – Excavated material takes up more space than it did in its natural state, affecting transportation and disposal planning.
By factoring in these volume changes, estimators can prevent miscalculations that lead to cost overruns or delays.
"Earthwork takeoff isn’t just about moving dirt—it’s about keeping your project on time and on budget. A small miscalculation in cut-and-fill volumes can lead to costly delays or material shortages. The best approach is to rely on accurate site data, use the right estimation methods, and always plan for material shrinkage and swell. Precision here sets the foundation for a smooth construction process." - - Ari Aarniovuori, Deployment & Support at Fondion
Common Methods for Earthwork Takeoff
1. Average End-Area Method
The average end-area method is a widely used technique for calculating earthwork volumes, especially in linear construction projects like roads and pipelines. It estimates the volume of material to be excavated or filled by averaging the cross-sectional areas of the earth at regular intervals along a project’s length and multiplying by the distance between them.
This method is preferred for several reasons:
- Simplicity – It requires only basic measurements of cross-sections and distances, making it easy to apply.
- Efficiency – It works well for projects with consistent cross-sections, reducing the need for complex calculations.
- Accuracy for Linear Projects – It provides reliable volume estimates when terrain changes are gradual and sections are evenly spaced.
However, accuracy depends on using appropriate intervals. Large gaps between sections can miss variations in the terrain, leading to miscalculations. To improve precision, sections should be taken at shorter, consistent intervals where the ground surface changes significantly.
2. Grid-Cell or Block Method
The grid-cell or block method divides a construction site into smaller, uniform sections to estimate earthwork volumes more precisely. Each section, or grid cell, is analyzed individually to determine the amount of material that needs to be excavated (cut) or added (fill).
By breaking the site into manageable units, this method helps improve accuracy and reduces the risk of overlooking variations in elevation or terrain.
This approach calculates cut and fill quantities for each grid cell separately, and then sums them to determine the total earthwork volume. Because each section is evaluated on its own, the method accounts for localized changes in elevation, making it particularly useful for projects with uneven terrain. It also provides a structured way to estimate material movement, which helps in planning equipment needs and scheduling work efficiently.
The grid-cell method is often used when working with digital terrain models (DTMs) or geographic information system (GIS) data, as it aligns well with modern software tools. By applying this structured approach, you can achieve more reliable earthwork estimates, minimizing costly miscalculations.
3. Cross-Section or Section Method
The cross-section or section method is a technique used to calculate earthwork volumes by analyzing vertical slices of a construction site. These slices, or cross-sections, are taken at regular intervals along the project's length.
By measuring the area of each slice and calculating the volume between them, you can determine the total amount of earth that needs to be excavated or filled.
This method improves accuracy in volume calculations by breaking down the site into smaller, manageable sections. Instead of estimating the entire area at once, you analyze each slice separately, which helps account for variations in terrain. The more cross-sections you take, the more precise your calculations will be.
Using the cross-section method helps in:
- Identifying changes in elevation and soil conditions along the project site.
- Providing detailed volume calculations for each section, reducing estimation errors.
- Ensuring more accurate planning for excavation and material movement.
Because this method offers a clear breakdown of earthwork quantities, it is widely used in road construction, pipeline projects, and other linear infrastructure developments where terrain changes frequently.
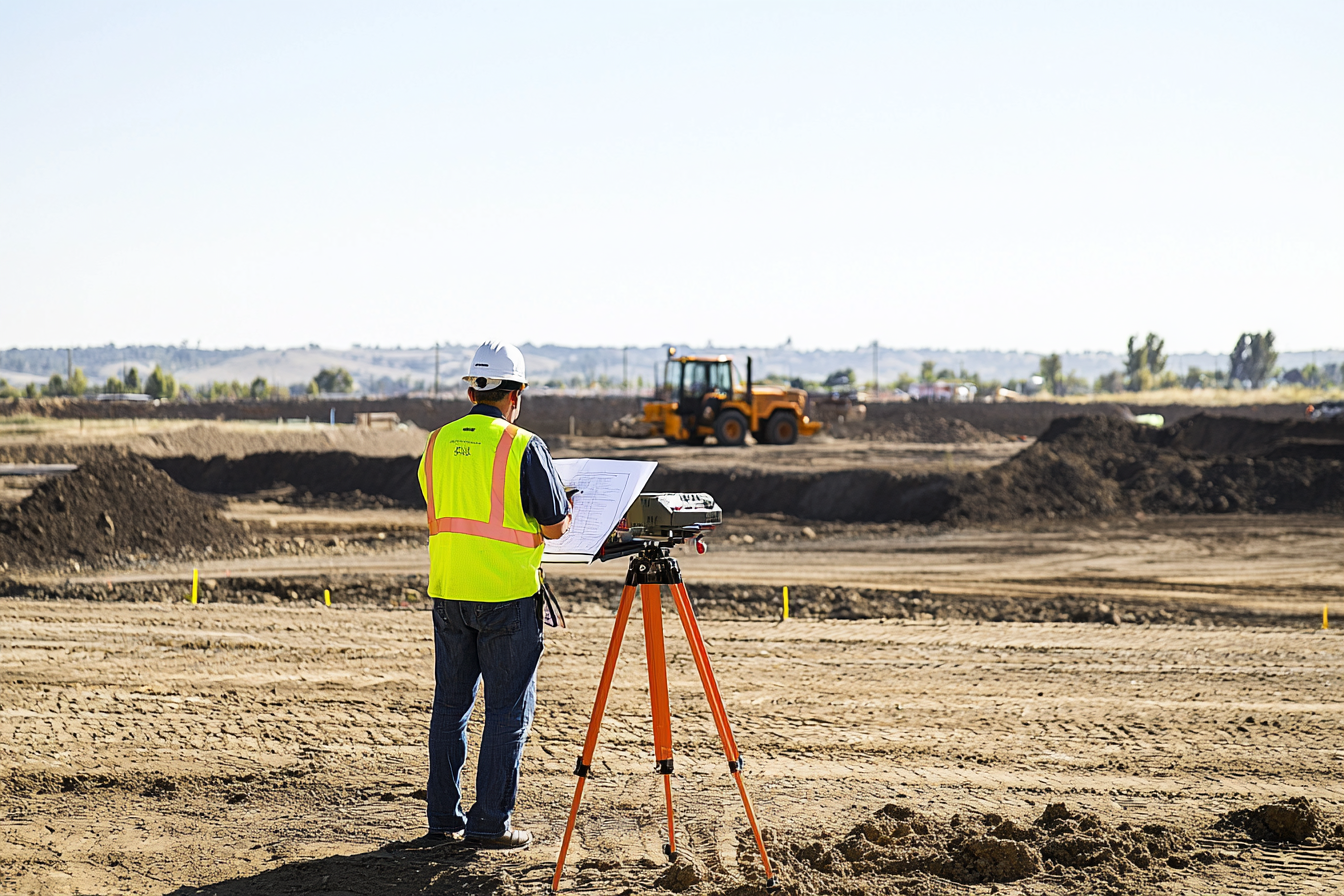
Best Practices for Accurate Earthwork Takeoff
1. Conduct Thorough Site Assessments
Begin by evaluating the site’s topography. Identify elevation changes, slopes, and natural drainage patterns, as these affect excavation and grading requirements. Next, analyze soil conditions.
Different soil types impact excavation difficulty, compaction rates, and material hauling needs. Review any potential obstacles like existing structures, underground utilities, or environmental restrictions that could complicate earthwork operations.
In addition to on-site inspections, study relevant documentation. Site plans and surveys provide baseline measurements and design specifications. Geotechnical reports provide insights into soil composition, groundwater levels, and stability concerns. These documents help anticipate challenges and refine takeoff calculations.
Skipping a detailed assessment increases the risk of miscalculations, leading to budget overruns and project delays. A comprehensive site evaluation lays the groundwork for accurate and reliable earthwork estimates.
2. Utilize Advanced Estimation Software
Modern estimation software improves the accuracy and efficiency of earthwork takeoff by automating complex calculations and minimizing human error. Manual methods often involve tedious measurements and calculations, increasing the risk of mistakes.
Software tools eliminate these issues by precisely analyzing digital plans and generating accurate volume estimates.
Using software also improves efficiency in several ways:
- Streamlined Data Input – Digital takeoff tools allow you to upload site plans directly into the software, reducing the time spent on manual data entry.
- Automated Volume Calculations – The software quickly determines cut-and-fill volumes, saving time compared to manual calculations.
- Integrated Reporting – Many programs generate detailed reports, making it easier to share takeoff results with project stakeholders.
Another advantage is the ability to replicate results for repetitive design elements, such as roads or building foundations. This prevents redundant work and ensures consistency across multiple sections of a project. Some software solutions also enable real-time collaboration, allowing multiple team members to work on the same takeoff simultaneously.
Fondion simplifies the entire estimation process by automating takeoffs, generating accurate cost-based calculations, and creating professional proposals. By using real company costs in estimations, Fondion helps businesses improve profit margins and eliminate costly miscalculations. With its intuitive interface and built-in CRM, it also enhances communication and project organization.
3. Regularly Update and Review Plans
Regularly updating and reviewing earthwork plans is important for maintaining accuracy throughout a construction project. Plans can change because of design modifications, unforeseen site conditions, or updated project requirements.
If these changes are not reflected in the takeoff, estimations might become inaccurate, leading to costly mistakes.
Failing to keep plans up to date can result in miscalculations in cut and fill volumes, potentially leading to:
- Ordering too much or too little material increases waste or causes delays.
- Incorrect excavation depths, which might require rework and additional labor.
- Misalignment with updated project schedules, impacting overall timelines and costs.
Reviewing plans regularly helps ensure that all calculations are based on the latest site data. This process minimizes the risk of errors and keeps the project aligned with actual site conditions, preventing unexpected costs and delays.
4. Collaborate with Experienced Professionals
Working with experienced professionals improves earthwork takeoff accuracy by ensuring calculations account for all necessary factors, reducing the risk of costly project overruns.
Professionals with extensive field experience can identify potential challenges early, such as unexpected soil conditions or grading issues, allowing for adjustments before construction begins.
Beyond accuracy, collaborating with skilled professionals streamlines the takeoff process. Their familiarity with industry standards and best practices allows for more efficient data collection and interpretation. This can lead to faster project timelines and better alignment between estimates and actual site conditions.
Key benefits of working with experienced professionals include:
- Reduced Errors – Experts can spot miscalculations or missing details that could impact cost and schedule.
- Improved Efficiency – Their knowledge expedites the takeoff process, minimizing delays.
- Better Decision-Making – They provide insights on material selection, excavation methods, and site preparation.
- Enhanced Coordination – Collaboration ensures that estimators, engineers, and contractors work with the same accurate data.
5. Account for Environmental and Site Variables
Weather conditions play a major role in excavation feasibility. Heavy rainfall can saturate the soil, making it unstable and harder to work with. In extreme cases, excessive moisture can lead to erosion, increasing the amount of material that needs to be moved.
On the other hand, extreme heat can dry out certain soil types, making excavation more difficult and requiring additional equipment or techniques.
Site-specific factors also impact earthwork requirements. Groundwater levels influence soil stability and determine whether dewatering systems are needed. High groundwater can complicate excavation, requiring pumps or drainage solutions to keep the work area dry.
Poor natural drainage can lead to water pooling, which might require additional grading or soil stabilization efforts.
Conclusion
Accurate earthwork takeoff is important for cost control, scheduling, and project success. It depends on choosing the right method, using reliable data, and utilizing modern tools. Small miscalculations can lead to budget overruns and delays, making attention to detail critical. A precise takeoff ensures that projects stay on track and resources are used efficiently. Investing time in accuracy upfront reduces risks and improves profitability.
Improve Your Earthwork Estimation Accuracy with Fondion
Fondion is a construction takeoff and estimating software designed to help construction professionals generate faster, more accurate estimates and improve profit margins. By automating quantity takeoffs, basing calculations on real company costs, and generating professional proposals, Fondion helps streamline project planning and execution.
With built-in CRM features, you can manage customer interactions, ensure timely follow-ups, and maintain better communication to keep projects moving efficiently. Fondion eliminates guesswork, enhances accuracy, and helps construction companies win more projects while maintaining profitability.
Start your free Fondion trial today and experience the power of precise takeoff and estimation!
FAQ
What Is Earthwork Takeoff?
Earthwork takeoff is the process of calculating the amount of soil, rock, or materials to be excavated or filled on a site. It helps with budgeting, resource planning, and scheduling. Using digital tools improves accuracy and reduces costly errors.
How To Take Off Earthwork?
Review project plans, calculate cut and fill volumes, and consider soil conditions and compaction factors. Use digital tools for precision and adjust for shrinkage and swell. Organize data for cost estimation and planning. Good construction estimating software creates professional tender documents automatically and with the right content. In that way, you can make sure that you win more projects and have better profit margins because the documents automatically create a detailed list of what is included in the project and what is not included in the project. This way customer satisfaction stays very high while simultaneously you’ll only do the work that you are supposed to do keeping your time schedule and costs on budget.
What Does Takeoff Mean in Construction?
A takeoff measures materials needed for a project. Earthwork takeoff focuses on soil and rock volumes for excavation or filling. Accurate takeoffs help with cost control and project efficiency.
What Is the Difference Between a Takeoff and an Estimate?
A takeoff quantifies materials, while an estimate calculates the total cost, including labor, equipment, and overhead. Takeoffs ensure accurate estimates to prevent budget overruns.
What Are the Common Mistakes in Earthwork Takeoff?
Mistakes include inaccurate site data, miscalculating volumes, ignoring soil conditions, and using outdated plans. To avoid errors, verify data, use reliable tools, and cross-check calculations. Make sure that you don’t have to manually enter data into different systems, but rather, you can manage all information from a single system. If you are using various systems, the system you choose, like Fondion, should act as the master. This way, you only need to set up projects in one software, which then syncs with other systems. This allows you to accurately estimate and monitor costs while ensuring that you can learn from historical data about your true costs, optimizing your operations for profitability across different areas.