Consistency and quality are make-or-break factors in construction projects. Without a solid plan in place, things can quickly spiral—leading to delays, cost overruns, or compliance issues. A well-structured quality management plan not only ensures the job gets done right but also keeps teams aligned and accountable. This article will explain how to create an effective quality management plan for your construction projects.
If you’re wondering what is construction project management, our article What Is Construction Project Management? A Complete Overview has all the details.
Importance of Quality Management Plans in Construction Projects
Quality management plans are important for ensuring construction projects meet client expectations, regulatory standards, and project specifications. These plans serve as a structured framework that guides teams in delivering work that aligns with predefined quality criteria.
By explicitly outlining quality benchmarks, they help maintain consistency across all phases of the project, from initial design to final delivery. Additionally, they ensure compliance with industry standards and local regulations, which is critical for avoiding costly legal or operational setbacks.
One of the key benefits of implementing a robust quality management plan is its role in minimizing delays, reducing costs, and preventing rework. With clear guidelines and proactive measures in place, quality-related issues can be identified and addressed early, before they escalate into larger problems.
1. Quality Objectives for Construction Projects
Define Quality Goals
To create effective quality goals for a construction project, start by making them specific. Avoid vague objectives like "ensure high quality" and instead define what "high quality" means in practical terms.
For example, this could include achieving zero structural defects, meeting all safety compliance standards, or completing work within specified tolerances. Specific goals reduce ambiguity and provide clarity for both the project team and stakeholders.
Measurability is also important. Goals should include quantifiable criteria that allow you to track progress and assess whether they are being met. Establishing measurable targets helps monitor performance and identify areas requiring improvement.
Finally, align these goals with the project’s scope, budget, and schedule. Unrealistic quality objectives can strain resources or delay timelines, while overly lenient ones might compromise project outcomes. Collaborate with stakeholders, including clients and regulatory bodies, to ensure goals are realistic and comprehensive.
Performance Metrics
When choosing performance metrics, focus on those that directly impact the quality objectives of your project. Common examples include:
- Defect Rates: Track the percentage of work that requires rework or corrections because of nonconformance with quality standards.
- Inspection Pass Rates: Measure how often inspections meet predefined criteria on the first attempt.
- Schedule Compliance: Monitor whether tasks are completed on time without compromising quality.
- Customer Satisfaction Scores: Evaluate feedback from clients to gauge whether the deliverables meet or exceed expectations.
- Material Wastage: Assess the volume of unused or discarded materials to identify inefficiencies in resource usage.
Each metric should be quantifiable and easy to track over time. For example, using inspection pass rates allows you to set thresholds that define acceptable performance levels. If pass rates fall below the threshold, it signals the need for corrective action or process adjustments.
Additionally, ensure that performance metrics are integrated into your quality management plan as part of regular monitoring activities. Use tools like checklists or software to document and analyze these metrics systematically.
Construction management software like Fondion helps streamline processes by providing tools for accurate takeoffs, real-cost estimates, and professional proposals, enabling better control over project performance and profitability.

2. Roles and Responsibilities in Quality Management
Quality Management Personnel
Key responsibilities of quality management personnel include overseeing all quality-related processes throughout the project lifecycle. This involves monitoring adherence to regulatory requirements, industry standards, and project-specific quality benchmarks.
By maintaining oversight, they ensure that every phase of the construction process aligns with predefined quality objectives.
Another critical function is addressing non-compliance issues instantly. When deviations or defects are detected, quality management personnel are responsible for investigating the root causes and implementing corrective measures.
This proactive approach minimizes the risk of recurring issues and ensures the project stays on track to meet quality expectations.
In addition, these individuals play a key role in maintaining clear communication regarding quality standards. They act as a link between the project team, stakeholders, and regulatory bodies, ensuring everyone understands the required guidelines and expectations.
Organizational Structure
By establishing a structured hierarchy, you can assign accountability at every level, from project managers to quality inspectors, fostering a culture of responsibility and adherence to quality protocols.
Key benefits of a robust organizational structure for quality management include:
- Defined Roles: Clearly outlining who is responsible for specific quality management tasks, such as inspections, approvals, or corrective actions.
- Effective Communication: Streamlining the flow of information between departments or teams, ensuring everyone is aligned on quality objectives.
- Accountability: Assigning ownership of quality-related outcomes to specific individuals or teams, reducing ambiguity.
- Resource Allocation: Ensuring that personnel, tools, and processes required for quality control and assurance are properly distributed and managed.
Additionally, the structure should support independence between quality management personnel and operational teams. This separation reinforces the integrity of quality oversight and prevents conflicts of interest.
An efficient organizational structure also supports compliance with industry standards like ISO 9001, which emphasizes leadership and the engagement of people. By embedding quality management roles into your structure, you ensure the processes align with these recognized benchmarks.
3. Quality Assurance (QA) Plan to Prevent Issues
Standards and Regulations
By adhering to established standards, you create a framework that guides every phase of the construction process, from design to completion, minimizing ambiguity and reducing the risk of costly rework or disputes.
Regulations such as building codes, safety mandates, and environmental laws provide the foundational criteria that have to be met for a project to proceed. Non-compliance can lead to penalties, delays, or even project shutdowns.
Additionally, standards like ISO 9001 offer structured principles—such as customer focus and evidence-based decision-making—that help streamline processes while maintaining high-quality outcomes.
Meeting these standards not only fulfills legal and contractual obligations but also improves client confidence and project reliability. Establishing a clear understanding of these benchmarks early in the project ensures all stakeholders are aligned and helps maintain accountability throughout the construction lifecycle.
QA Activities
One critical QA activity involves conducting regular audits. Audits assess whether construction processes align with the project’s quality management plan and regulatory requirements. They can identify gaps in compliance, helping you address deficiencies early.
Inspections are another key component of QA. These involve systematic evaluations of work in progress to ensure quality benchmarks are met. Inspections can focus on specific stages, such as foundation pouring or structural framing, and follow predefined criteria to maintain consistency. A detailed inspection plan increases transparency and ensures no critical steps are overlooked.
In addition to audits and inspections, process reviews evaluate the effectiveness of the workflows and methodologies used in construction. These reviews assess whether processes are efficient and whether they align with project objectives.
Each activity plays a distinct role in identifying and resolving potential issues early, ultimately supporting the delivery of a high-quality final product.
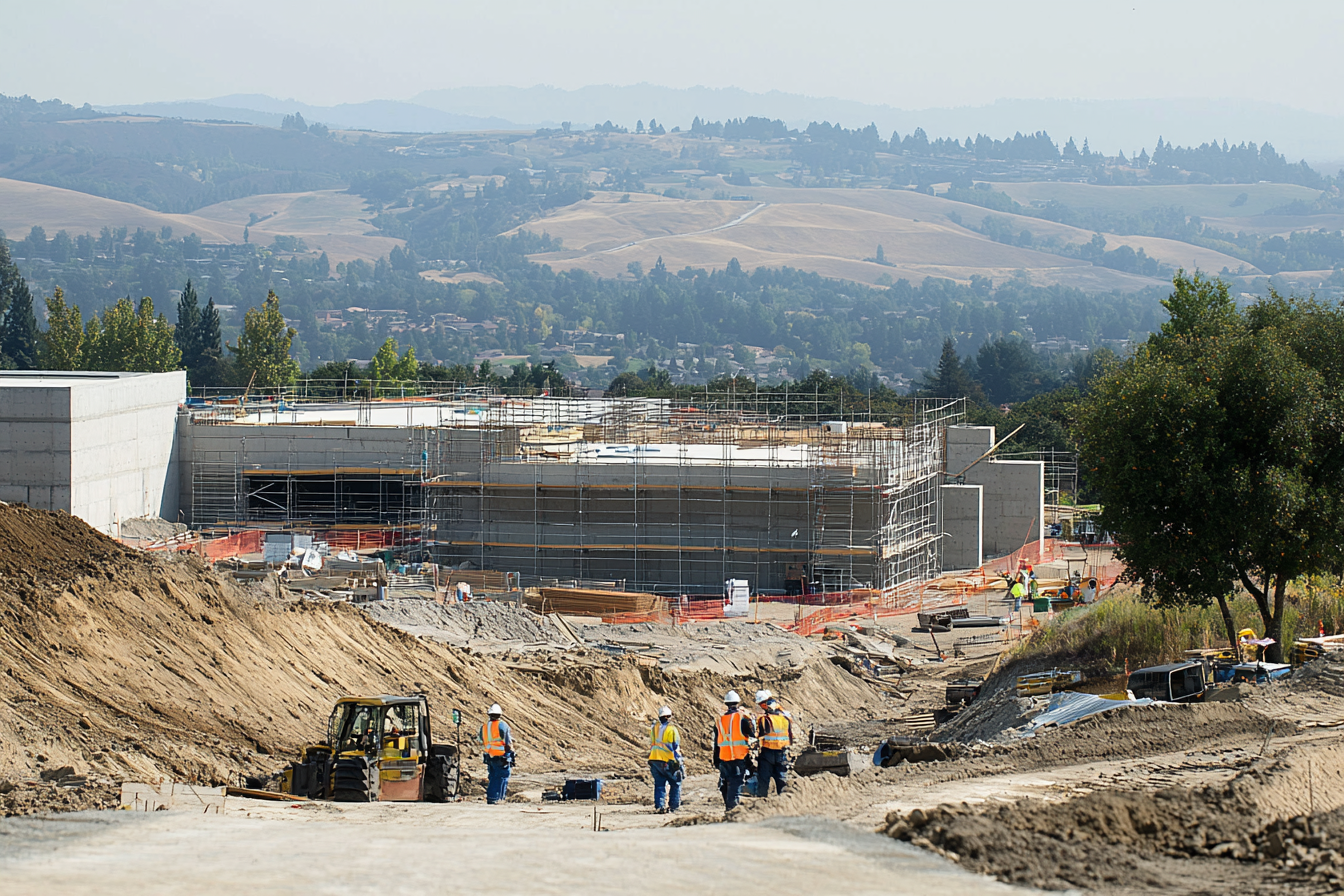
4. Quality Control (QC) Plan to Ensure Standards
Inspection and Testing Procedures
Through inspections, you can systematically evaluate different aspects of the construction process to confirm compliance with design requirements, regulatory standards, and client expectations.
Inspections are typically conducted at critical stages of the project, such as foundation work, structural framing, or system installations, and help detect deviations early. This allows you to address issues before they escalate into costly rework or delays.
Testing, on the other hand, focuses on verifying the performance and durability of materials and systems. Examples include compressive strength tests for concrete, weld quality checks for steel, and pressure tests for plumbing systems.
These evaluations are necessary to confirm that the materials used meet the required specifications and can perform as intended under operational conditions.
To streamline the process, many teams use standardized checklists that outline specific inspection criteria and acceptable results. This not only ensures consistency but also reduces the risk of overlooking critical aspects.
Additionally, technology, such as digital inspection tools, can improve accuracy and efficiency by automating data collection and reporting.
Documentation
Thorough documentation is important for tracking and ensuring compliance with quality requirements in construction projects. It is concrete evidence that your processes and outputs adhere to both quality standards and project specifications.
Without well-maintained documentation, demonstrating compliance to clients, regulators, or other stakeholders becomes challenging, and gaps in accountability might arise.
To ensure effective documentation, consider these practices:
- Record compliance with regulatory standards: Maintain detailed records that confirm adherence to industry codes, environmental regulations, and safety standards relevant to your project.
- Document project specifications: Capture how the project meets contract requirements, including materials used, design tolerances, and construction methods.
- Log inspection and testing results: Keep a clear record of all inspection findings and test outcomes, which can help verify that construction processes and deliverables meet quality criteria.
- Track corrective actions: Document any quality issues identified and the steps taken to resolve them. This creates a trail of accountability and ensures continuous improvement.
- Centralize access to quality records: Use digital tools to store and organize documentation, making it easier for team members and stakeholders to retrieve information when needed.
Corrective Actions
Corrective actions help fix quality issues and stop them from happening again. By finding and solving the root cause of a problem, instead of just addressing the symptoms, you can avoid similar issues in the future.
This saves time, and resources, and ensures better quality. Documenting the steps taken and improving processes like checklists and training also strengthens quality management and builds long-term success.
5. Communication Plan for Quality Updates
Quality Meetings
Quality meetings are important for maintaining alignment among all project stakeholders on quality-related matters. They serve as a structured platform to discuss ongoing issues, review progress, and ensure compliance with established quality standards.
By fostering open communication, these meetings help identify potential challenges early, enabling proactive solutions that prevent defects and delays.
During these meetings, you can address several key aspects of quality management:
- Progress Updates: Review the status of ongoing quality assurance and control activities to ensure tasks are on track.
- Issue Resolution: Identify quality concerns or deviations from standards and assign responsibilities for corrective actions.
- Policy Reinforcement: Reiterate project-specific quality requirements, regulatory guidelines, and client expectations to maintain focus.
- Stakeholder Feedback: Provide a space for stakeholders to voice concerns or suggest improvements, fostering collaboration.
- Future Planning: Discuss upcoming milestones and align on quality benchmarks to ensure preparedness.
Reporting Protocols
Establishing structured reporting protocols is important for maintaining clarity and accountability in quality management. By implementing a reliable system to record and distribute reports, you ensure stakeholders remain informed, enabling them to make timely and effective decisions.
To achieve this, follow these key practices:
- Define Distribution Channels: Identify the most effective ways to share reports, such as email, project management software, or cloud-based platforms. Ensure these methods are secure and accessible to all relevant parties.
- Set Reporting Schedules: Establish a consistent timeline for report submission, whether daily, weekly, or at key project milestones. This predictability minimizes delays and ensures stakeholders receive updates when needed.
- Standardize Report Formats: Use uniform templates for all reports to streamline documentation and make data easier to interpret. Include sections for inspection results, compliance status, corrective actions, and progress tracking.
- Assign Responsibilities: Clearly designate who is responsible for preparing, reviewing, and distributing each type of report. Accountability reduces the risk of missed communication.
- Enable Real-Time Accessibility: Utilize tools that allow stakeholders to access reports in real time, fostering immediate action on critical issues. This is particularly useful for large projects where delays can have significant consequences.
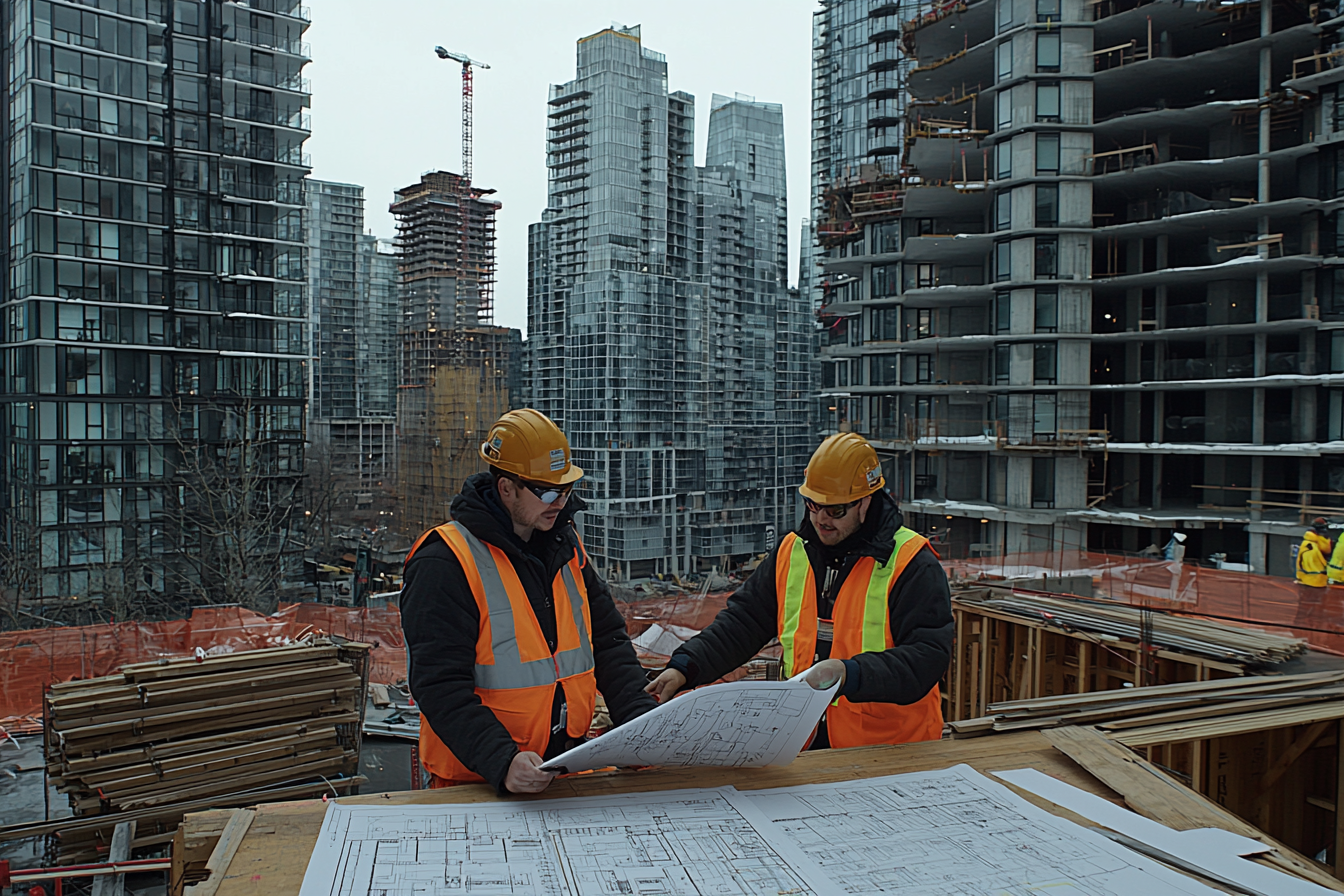
6. Continuous Improvement for Better Results
Continuous improvement focuses on refining processes, addressing recurring issues, and enhancing project outcomes. By gathering feedback from stakeholders, analyzing inspection results, and fostering open communication, teams can pinpoint areas for improvement.
Proven methods like Continuous Improvement (CI), Kaizen, Six Sigma, and Lean Management help reduce inefficiencies, resolve problems, and boost quality.
Documenting feedback, updating training, and monitoring outcomes ensure that lessons learned are applied, building a culture of ongoing improvement for current and future projects.
7. Risk Management for Quality Control
Risk management helps identify, assess, and address potential issues that could impact quality. By evaluating risks based on their likelihood and impact, teams can prioritize critical threats and allocate resources effectively.
Mitigation strategies include contingency planning, monitoring systems, and proactive communication to prevent disruptions. Using tools like risk matrices, predictive analytics, and real-time tracking ensures risks are managed efficiently, maintaining quality throughout the project.
8. Review and Approval of the Plan
Reviewing the quality management plan ensures it aligns with project goals, standards, and regulatory requirements. This involves cross-referencing the plan with deliverables, quality objectives, and compliance guidelines like ISO 9001 and local building codes.
A thorough review confirms that all procedures, tools, and methodologies, such as inspection schedules and corrective actions, are well-documented and ready for implementation.
Approval signatures formalize stakeholder agreement and accountability for the plan. By signing off, all parties commit to adhering to the outlined processes and meeting quality standards. This shared acknowledgment reduces disputes, fosters collaboration, and ensures everyone is aligned on maintaining quality throughout the project.
Conclusion
A quality management plan is both a roadmap to achieving excellence and a safeguard against costly failures in construction projects. Its success hinges on clear objectives, defined roles, robust QA/QC processes, and ongoing improvement efforts.
By integrating quality into every stage, you not only meet standards but also build trust, reduce risks, and deliver enduring results.
Fondion makes it easier to manage construction projects by offering fast and accurate takeoffs, real-cost estimates, and professional proposals. With tools designed for modern construction needs, Fondion helps you enhance customer communication and improve profit margins. Take the guesswork out of estimating and set your projects up for success.
Start your free Fondion trial today and experience a smarter way to manage your construction projects.
FAQ
How Do You Write a Quality Plan for a Construction Project?
Define objectives, scope, and standards; outline roles and processes for quality assurance and control; include inspection, testing, and documentation protocols; reference standards and client requirements; and establish a communication and continuous improvement plan. Good construction estimating software creates professional tender documents automatically and with the right content. In that way, you can make sure that you win more projects and have better profit margins because the documents automatically create a detailed list of what is included in the project and what is not included in the project. This way customer satisfaction stays very high while simultaneously you’ll only do the work that you are supposed to do keeping your time schedule and costs on budget.
How Do You Develop a Quality Management Plan for a Project?
Set clear objectives, identify stakeholders, outline roles, establish standards and inspection criteria, schedule audits, use templates for consistency, and include communication and improvement processes.
What Is Quality Management in a Construction Project?
Quality management ensures all activities, materials, and processes meet standards, client expectations, and regulatory requirements through planning, control, assurance, and improvement.
What Is a QC Plan in Construction?
A QC plan details procedures, standards, inspections, testing methods, corrective actions, and communication protocols to ensure project quality compliance.
What Are the Key Components of a Construction Quality Management Plan?
Key components include objectives, roles, standards, quality control processes, inspection/testing procedures, corrective actions, documentation, and continuous improvement strategies. Make sure that you don’t have to manually enter data into different systems, but rather, you can manage all information from a single system. If you are using various systems, the system you choose, like Fondion, should act as the master. This way, you only need to set up projects in one software, which then syncs with other systems. This allows you to accurately estimate and monitor costs while ensuring that you can learn from historical data about your true costs, optimizing your operations for profitability across different areas.