Ordering the wrong amount of drywall can cause major project setbacks. If you underestimate materials, you risk delays and unplanned purchases. If you overestimate, you waste money and storage space. A precise drywall takeoff helps avoid these issues by calculating the exact materials needed before ordering.
By following the right approach, you can eliminate miscalculations, reduce material waste, and keep your project on track. This article outlines a structured process to help you perform an accurate drywall takeoff and avoid common mistakes.
Want to know more about material takeoffs? Check out "A Comprehensive Guide to Material Takeoffs for Construction Projects."
Importance of Drywall Takeoff
A drywall takeoff is the process of calculating the number of drywall sheets and related materials required for a construction project. It involves reviewing blueprints, measuring wall and ceiling dimensions, and considering material waste to ensure accurate estimates. This process prevents shortages, unnecessary costs, and delays, making it a crucial step in project planning.
Key benefits of an accurate drywall takeoff:
- Prevents material shortages that can halt progress.
- Avoids over-ordering, reducing waste and extra costs.
- Ensures proper budgeting by providing clear cost estimates.
- Improves project efficiency by having the right materials on-site from the start.
- Helps meet project deadlines by eliminating last-minute supply issues.
"Performing a drywall takeoff is all about precision and attention to detail. When you take the time to measure accurately and account for every material needed, you not only save money but also ensure a smoother construction process. At Fondion, we believe that the right tools and a thoughtful approach can make all the difference in delivering a successful project." — Ari Aarniovuori, Deployment & Support at Fondion
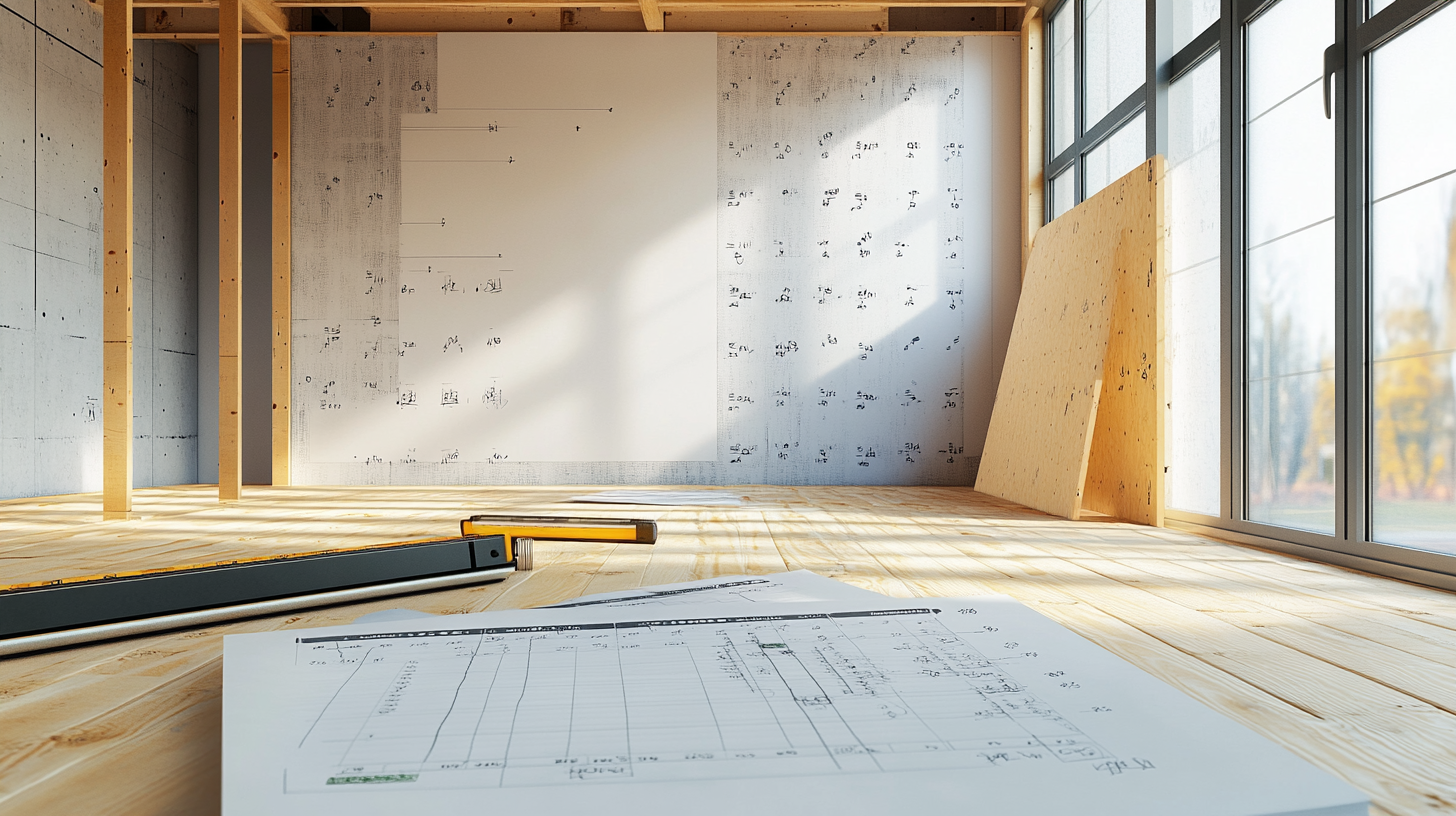
Step-by-Step Process for an Accurate Drywall Takeoff
Step 1: Review the Construction Plans
Start by identifying the dimensions on the blueprints. Architectural plans typically provide wall elevations and ceiling layouts, showing precise measurements. If any measurements are missing or unclear, use the plan’s scale to estimate proportions. Misinterpreting dimensions can lead to material miscalculations, so verifying all measurements before proceeding is crucial.
Next, analyze wall and ceiling types to determine specific drywall requirements. Some walls require multiple layers for fire resistance or soundproofing, while others may have large openings for doors and windows that reduce the amount of drywall needed. Understanding these details prevents over-ordering and ensures compliance with building regulations.
Check the drywall specifications provided in the plans. Different areas may require moisture-resistant drywall (for bathrooms and kitchens) or fire-rated drywall (for garages and shared walls in multi-unit buildings). Choosing the wrong type can lead to costly rework and potential safety issues.
Finally, organize measurements for accuracy by categorizing data by room or section. Record wall heights, lengths, and ceiling areas separately to avoid confusion. Keeping measurements structured minimizes errors and simplifies the process of calculating material quantities.
Step 2: Measure Wall and Ceiling Areas
Begin with wall measurements by determining the height and length of each wall from floor to ceiling. If a wall includes doors or windows, measure their width and height separately. Since these areas do not require drywall, excluding them from total calculations prevents over-ordering.
For ceiling measurements, determine the length and width of each section. If the ceiling has sloped or irregular shapes, break it into smaller rectangles and calculate each section separately. This ensures that all ceiling areas are accounted for without miscalculations.
Once all measurements are recorded, calculate the total drywall coverage using these formulas:
- Wall area = Length × Height
- Ceiling area = Length × Width
Subtract the total area of doors, windows, and large openings from the wall and ceiling measurements to get the net drywall coverage area. This final number determines the exact amount of drywall sheets required for the project, preventing excess waste and unexpected material shortages.
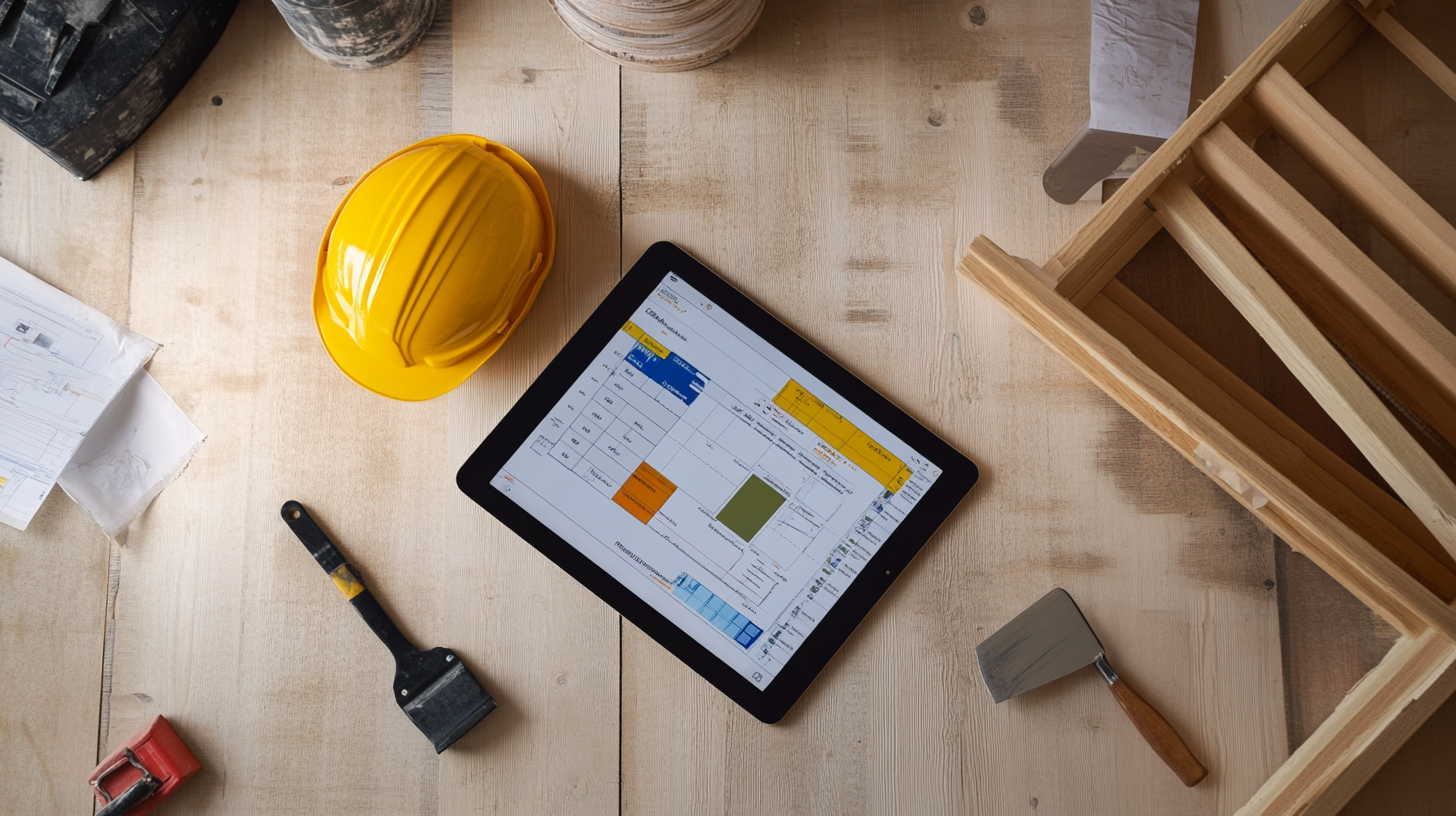
Step 3: Determine Drywall Sheet Quantities
Calculating the correct number of drywall sheets ensures that you have enough material without unnecessary excess. Ordering too little can delay the project while ordering too much increases costs and storage issues. Proper planning minimizes waste and ensures a smooth installation process. To determine the required drywall sheets, divide the total wall and ceiling square footage by the area of a single drywall sheet. Standard sizes include:
- 4×8 feet (32 sq. ft.) – Common for residential projects, easy to handle.
- 4×10 feet (40 sq. ft.) – Reduces seams, preferred for taller walls.
- 4×12 feet (48 sq. ft.) – Covers larger areas with fewer joints but requires more effort to handle.
Since drywall sheets cannot always be used in full, always round up to the next whole number to account for full coverage.
Accounting for Waste and Offcuts is also critical. Cutting drywall to fit around doors, windows, electrical boxes, and irregular spaces creates excess material. To prevent shortages, add a 5-10% waste factor depending on the complexity of the layout. Having a buffer helps avoid last-minute reordering, ensuring a faster and more efficient installation.
Step 4: Calculate Joint Compound, Tape, and Fasteners
Estimating Joint Compound – This material is used to cover seams and screw indentations for a smooth finish. For a standard three-coat application, plan for approximately 1.5 to 2 gallons per 100 square feet of drywall. If working with textured finishes or thick applications, additional compounds may be required.
Calculating Drywall Tape – Since drywall sheets are 4 feet wide, seams are inevitable. To estimate the required tape, measure the total linear feet of seams. A standard drywall project requires one roll of tape per 500 linear feet. Using paper tape is common, but fiberglass mesh tape is a stronger option for high-moisture areas or areas prone to cracks.
Determining Fastener Quantities – Drywall is secured with screws or nails, with the required amount depending on stud spacing and sheet size. A 4×8 drywall sheet typically requires 32 screws when attached to wood studs, while a 4×12 sheet needs around 48 screws for proper stability. If using metal framing, screws should be spaced closer together, increasing the total quantity required.
By keeping a structured material list and cross-checking quantities, you can reduce waste, improve efficiency, and keep your project on schedule. Proper planning prevents unnecessary trips to the supplier and ensures a seamless drywall installation process.
Step 5: Create a Detailed Material List
A well-structured material list ensures that all necessary drywall components are accounted for, reducing the risk of delays, miscalculations, or budget overruns. Listing materials in advance helps streamline procurement and keeps installation on schedule.
Start by identifying the drywall sheets required based on the project’s needs. Standard 4×8 sheets are commonly used, but 4×10 or 4×12 sheets can reduce seams and improve finishing quality. Some areas may require moisture-resistant drywall for bathrooms, fire-rated drywall for garages, or soundproof drywall for noise reduction. Choosing the correct type prevents compliance issues and ensures a durable installation.
Beyond drywall sheets, include essential installation materials:
- Joint compound – Required for covering seams and screw indentations. Choose between all-purpose, setting-type, or lightweight compound based on project requirements.
- Drywall tape – Paper tape is standard, but fiberglass mesh tape offers better crack resistance in high-stress areas.
- Fasteners – Drywall screws are standard for securing sheets to studs, but some projects may require nails based on framing material. Choose the right screw length according to drywall thickness.
- Corner beads – Protects and reinforces outside corners. Options include metal, vinyl, or paper-faced corner beads.
- Adhesives – In some installations, adhesives reduce the need for excess fasteners and provide stronger bonding.
For a complete takeoff, consider additional supplies that impact installation efficiency:
- Backing materials – Needed for unsupported joints or framing areas requiring reinforcement.
- Primer and sealants – Essential for preparing drywall surfaces before painting or finishing.
- Tools and accessories – While not part of the material takeoff, ensure you have taping knives, sanding sponges, a utility knife, and a drywall lift for easier handling.
To avoid shortages, organize the list by category and quantity and cross-check against project measurements. Factoring in waste percentages (typically 5-10%) ensures you have enough material without excessive overages. A detailed and accurate material list improves efficiency, keeps costs under control, and ensures smooth project execution.
Using reliable construction takeoff software like Fondion can simplify the drywall takeoff process by automating material calculations and reducing errors. Fondion helps contractors accurately estimate drywall sheets, fasteners, and finishing materials, ensuring projects stay on budget and on schedule. By streamlining takeoff and procurement, Fondion improves efficiency and minimizes waste.
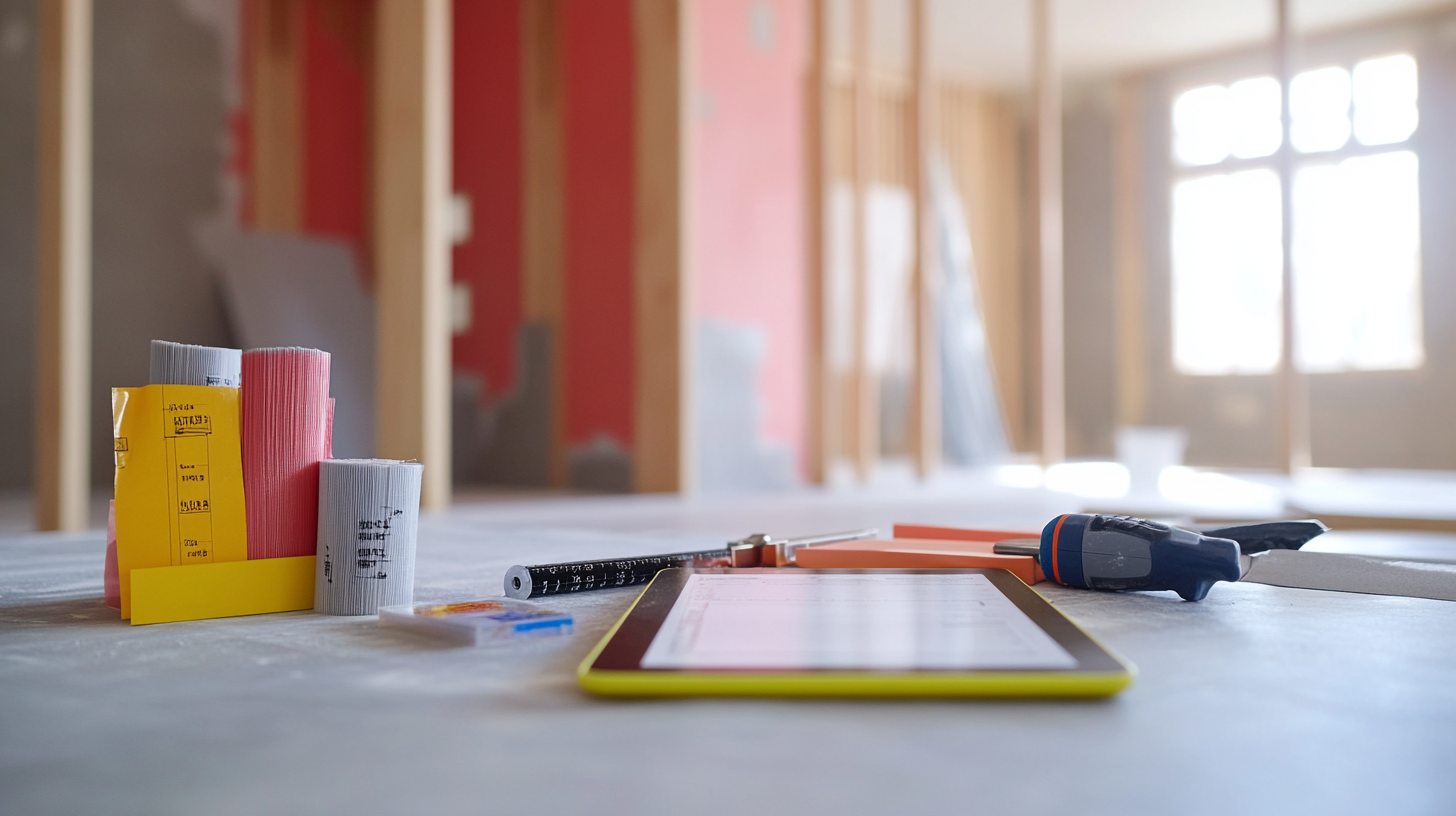
Common Mistakes to Avoid in Drywall Takeoff
One of the biggest mistakes is misinterpreting construction plans. Drywall takeoff relies on accurate measurements from blueprints, but missing details like wall heights, ceiling slopes, or special framing requirements can result in ordering the wrong amount of materials. Solution: Always cross-check measurements with architectural plans and, when in doubt, consult the project team to verify unclear dimensions before finalizing estimates.
Another common error is failing to account for waste. Drywall sheets often require cuts to fit around doors, windows, and irregular wall shapes, leading to excess material waste. If not factored in, you might run short on materials. Solution: Include a 5-10% waste buffer in your calculations, depending on project complexity, to ensure a sufficient supply without excessive overages.
Overlooking additional materials such as joint compound, tape, and fasteners is another frequent issue. Many estimates focus only on drywall sheets, forgetting the necessary finishing supplies. Solution: Create a complete material list, including joint compound for seams, tape for reinforcement, and the correct fastener type and quantity for wood or metal framing.
Relying on manual calculations increases the risk of human error. Estimating drywall quantities by hand can lead to miscounts, miscalculations, or overlooked sections. Solution: Use takeoff software to automate calculations, improve accuracy, and reduce time spent on manual counting. Tools like Fondion streamline the process by providing real-time adjustments and material tracking.
Lastly, ignoring project-specific drywall requirements can result in compliance issues or poor performance. Some areas, like bathrooms, garages, or shared walls in multi-unit buildings, require moisture-resistant, fire-rated, or soundproof drywall. Solution: Always review building codes and project specifications to ensure you’re selecting the correct drywall type for each section of the project.
Conclusion
A precise drywall takeoff is essential for efficient material planning, cost control, and smooth project execution. Miscalculations can lead to delays, material shortages, or unnecessary expenses, making accuracy a top priority.
To ensure reliable estimates, it's crucial to pay attention to detail, regularly update supplier prices, and account for material waste. Factoring in waste allowances and project-specific drywall requirements helps prevent last-minute shortages and unexpected costs.
A well-executed takeoff streamlines procurement reduces excess ordering, and keeps projects on schedule, ensuring a cost-effective and efficient construction process.
Improve Accuracy and Efficiency in Your Drywall Takeoff with Fondion
Fondion is an advanced construction takeoff software designed to simplify drywall estimating by automating calculations and reducing errors. With Fondion, contractors can ensure precise material estimates, improved cost control, and efficient project planning. By integrating digital tools, you can eliminate manual errors and streamline procurement for a smoother workflow.
Start your free Fondion trial today and experience a faster, more accurate, and hassle-free drywall takeoff process.
FAQ
What Is a Drywall Takeoff?
A drywall takeoff is the process of calculating the materials needed for a construction project, including drywall sheets, joint compound, screws, and tape. It involves measuring wall and ceiling dimensions, accounting for openings like doors and windows, and factoring in waste to ensure accurate material estimates.
What Are the Basic Steps Involved in a Drywall Takeoff?
Begin by reviewing project plans to identify areas needing drywall and measure wall and ceiling dimensions, excluding openings like doors and windows. Calculate total square footage and determine the number of drywall sheets required, factoring in waste and cutting allowances. Include additional materials such as joint compound, tape, fasteners, and corner beads, and consider any special requirements like fire-rated or moisture-resistant drywall. Verify calculations for accuracy, then compile a comprehensive material list to streamline ordering and installation.
What Tools Do I Need for a Drywall Takeoff?
For a drywall takeoff, you'll need a measuring tape or digital laser measurer for accurate dimensions, a notepad or spreadsheet to record measurements, and a calculator for material estimations. Construction plans or blueprints are essential for referencing wall and ceiling areas while estimating software can streamline calculations and reduce errors. A scale ruler helps interpret drawings, and highlighters or colored markers can differentiate sections. Having a drywall material list on hand ensures you don't overlook anything. These tools will help you efficiently determine the materials needed for your project.
How Can Estimating Software Improve My Drywall Takeoff?
Good construction estimating software creates professional tender documents automatically and with the right content. In that way, you can make sure that you win more projects and have better profit margins because the documents automatically create a detailed list of what is included in the project and what is not included in the project. This way customer satisfaction stays very high while simultaneously you’ll only do the work that you are supposed to do keeping your time schedule and costs on budget.
What Features Should I Look for in Drywall Estimating Software?
Make sure that you don’t have to manually enter data into different systems, but rather, you can manage all information from a single system. If you are using various systems, the system you choose, like Fondion, should act as the master. This way, you only need to set up projects in one software, which then syncs with other systems. This allows you to accurately estimate and monitor costs while ensuring that you can learn from historical data about your true costs, optimizing your operations for profitability across different areas.