Miscalculating lumber can lead to wasted materials, increased costs, and unexpected project delays. Ordering too much results in unnecessary expenses, while ordering too little causes interruptions that slow down construction. Accurate planning is essential to keep projects efficient and cost-effective.
A lumber takeoff ensures the right amount and type of wood is used, preventing shortages and excess purchases. By carefully estimating materials, builders can stay within budget and maintain a smooth workflow. This article outlines the essential steps to perform a precise lumber takeoff for construction success.
To learn more about material takeoffs, read "A Comprehensive Guide to Material Takeoffs for Construction Projects."
Understanding Lumber Takeoff
A lumber takeoff is the process of calculating the exact amount and types of wood needed for a construction project. It ensures that builders have the right materials in the right quantities, preventing shortages and excess purchases. This step is crucial for keeping projects on schedule and within budget.
By carefully reviewing construction plans, you can optimize material usage, control costs, and improve efficiency. A well-executed takeoff reduces waste and ensures smooth project execution. Here are the key benefits of a lumber takeoff:
- Accurate Material Estimation – Determines the precise amount of lumber for framing, sheathing, and structural components.
- Cost Control & Budgeting – Helps estimate costs accurately, reducing the risk of budget overruns.
- Minimized Waste – Reduces excess materials and promotes sustainable building practices.
- Efficient Construction Planning – Prevents project delays caused by under-ordering or over-ordering materials.
"A precise lumber takeoff isn’t just about numbers—it’s about keeping your project on track, minimizing waste, and staying within budget. The right tools and a careful approach make all the difference." — Sanni Bomberg, Product Specialist at Fondion
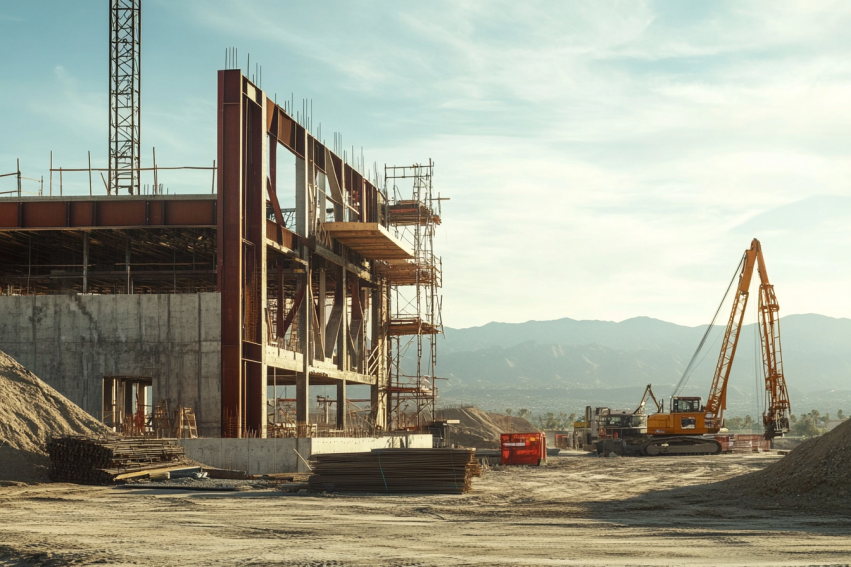
Step-by-Step Process for an Accurate Lumber Takeoff
.A systematic approach is important to avoid missing critical details in a lumber takeoff plan. A detailed step-by-step procedure is discussed below.
Step 1: Review the Construction Plans
The first step is identifying all structure parts that require lumber. These include walls, floors, ceilings, and roofs, each of which has different material requirements. Load-bearing walls, for instance, support the building’s weight and require stronger, thicker lumber, whereas non-load-bearing partitions can use lighter materials.
Skipping this step can result in using the wrong type of wood, which may compromise the building’s stability.
After identifying the structural components, review the construction drawings to determine the exact measurements and spacing of framing materials. If wall studs are placed 16 inches apart, you can calculate the total number required by dividing the wall length by this spacing and adding extra pieces for openings such as doors and windows.
Similarly, for flooring, roof rafters, and beams, spacing specifications must be cross-checked with the plans to ensure accurate calculations. Missing these details can lead to either under-ordering or over-ordering materials, increasing costs and project waste.
Some structures have design elements that require additional planning, such as vaulted ceilings, stair openings, large window spans, or multi-floor load transfers. These features often need reinforced beams or engineered wood products, like laminated veneer lumber (LVL), to provide extra strength.
If these details are overlooked, the initial lumber takeoff may not account for necessary reinforcements, resulting in mid-project adjustments that can disrupt timelines and budgets.
Using digital blueprint software can help streamline the review process by allowing precise measurements and reducing human error. Additionally, color-coding different sections on the plans can help differentiate materials for framing, sheathing, and structural support, making it easier to visualize material distribution.
Step 2: Identify and Categorize Lumber Needs
Classifying lumber correctly ensures that the right materials are used for both structural strength and finishing details. A well-organized classification helps you avoid ordering mistakes and ensures smooth construction.
Lumber is primarily categorized based on function. Framing lumber is used for structural support in walls, floors, and ceilings while finishing lumber is for decorative elements like trim and molding. Identifying these differences helps in selecting the right material for each section of the project.
Each piece of lumber also has a size and grade. Lumber is often labeled with nominal sizes like 2x4 or 2x6, but these dimensions are slightly smaller after processing. Strength grading, determined by factors like wood species and defects, ensures the wood is strong enough for load-bearing structures. Checking size and grade helps in meeting building code requirements and maintaining structural integrity.
Lumber selection depends on its intended application. Dimensional lumber is commonly used for framing, plywood, and OSB (oriented strand board) serves as sheathing and subflooring, and pressure-treated wood is required for moisture-exposed areas like decks.
Engineered wood such as laminated veneer lumber (LVL) and I-joists provide extra strength for beams and large spans. Trim and finish wood are used for doors, windows, and decorative work.
Before placing an order, always compare the material list with the construction plans. Any mismatch in lumber type, size, or grade can lead to waste, costly reorders, or weak construction. Using digital takeoff software can help organize materials more efficiently and prevent errors.
Step 3: Measure and Quantify Materials
Accurate measurements are the foundation of a precise lumber takeoff. Errors in calculations can lead to material shortages, delays, or overspending on unnecessary lumber. To avoid this, measurements must be taken carefully, considering both linear feet and board feet depending on the type of lumber being used.
Linear feet are the total length of lumber needed. This unit is commonly used for materials like studs, beams, and planks that come in standard lengths. To calculate linear feet, add up the length of all the required pieces for each lumber type. This ensures you order enough material without unnecessary surplus.
Board feet measure the volume of lumber, often used for rough-sawn wood and dimensional lumber that may be cut to size. The formula to calculate board feet is:
Board Feet = (Thickness in inches × Width in inches × Length in feet) ÷ 12
This method is essential for bulk purchases, ensuring you get the right quantity while minimizing waste.
To improve accuracy, always refer to the construction plans and list out every wood component needed. Group lumber by size and type, such as 2x4s, 2x6s, and plywood sheets, and measure each one systematically.
Use the correct unit of measurement based on how the supplier sells the material—some lumber is priced by board feet, while others are sold by piece count.
Double-check all calculations before placing an order. Small errors in measurements can multiply across a project, causing unexpected shortages or excess costs. Using digital takeoff tools can simplify this process by automating calculations and reducing manual errors.
Step 4: Convert Measurements to Quantities
After measuring and quantifying materials, the next step is to convert raw measurements into standardized units for ordering and budgeting. This ensures that the right amount of lumber is purchased without over- or underestimating needs, helping to control costs and prevent shortages.
Lumber is typically measured in linear feet, but suppliers often sell it in board feet or by piece count. To convert linear feet into board feet, use the formula:
Board Feet (BF) = (Thickness in inches × Width in inches × Length in feet) ÷ 12
For example, a 2×6 board that is 10 feet long would be calculated as (2 × 6 × 10) ÷ 12 = 10 board feet. Understanding this conversion ensures accurate ordering and cost estimation.
For sheet goods like plywood or oriented strand board (OSB), measurements are based on square footage. A standard 4×8 plywood sheet covers 32 square feet, so if a project requires 320 square feet of sheathing, 10 sheets would be needed. This method ensures accurate sheet material estimation.
Accounting for waste is also important. Waste can result from cutting, defects, and offcuts, and most projects include a 5-15% waste factor depending on complexity. Adding this percentage to calculations prevents material shortages and ensures smooth workflow.
Step 5: Create a Material List
A detailed material list is essential for smooth procurement and cost control. It ensures that the right type and quantity of lumber is ordered, preventing shortages and excess stock that could lead to budget overruns.
Each material entry should include a clear description, specifying the dimensions, length, and wood type. For example, instead of listing "lumber," it should state "2×4 pressure-treated pine, 10 feet long." This level of detail helps prevent ordering mistakes.
The quantity of each type of lumber should be listed based on takeoff calculations. This ensures accurate procurement, minimizing the risk of over-ordering or running short on materials.
Units of measurement should be standardized, using board feet, linear feet, or piece count as needed. Suppliers use these units to price materials, so aligning with their system ensures smooth transactions.
Including the unit cost per item allows for accurate cost estimation and comparison. Once the total cost per item is calculated (unit cost × quantity), budgeting becomes clearer, helping contractors stay within financial limits.
Finally, identifying reliable suppliers for each material ensures consistency in quality, pricing, and availability. Having a predefined list of suppliers streamlines the ordering process, reducing the risk of delays due to stock shortages.
Incorporating Fondion's construction management software into your workflow can significantly enhance the accuracy and efficiency of your lumber takeoff process. Fondion streamlines tasks like reviewing construction plans, measuring materials, and creating detailed material lists, ensuring precise estimates and effective project management.
By automating these steps, Fondion helps prevent costly errors, reduces material waste, and keeps your projects on schedule and within budget. Explore how Fondion can transform your construction planning and execution.
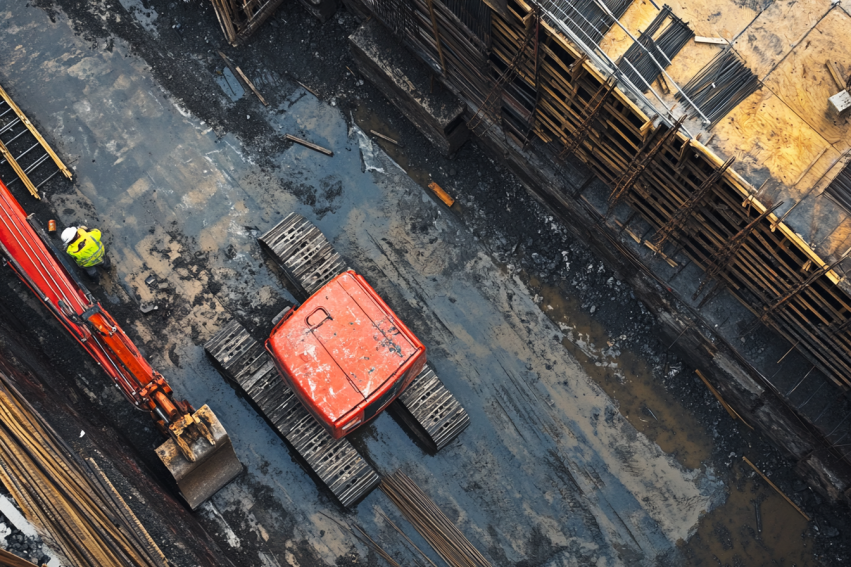
Common Mistakes to Avoid in Lumber Takeoff
One major mistake is not considering regional material availability when selecting lumber. Construction plans often specify materials that may not be easily accessible in certain locations, leading to delays or the need for last-minute substitutions. The best way to prevent this issue is to consult with local suppliers before finalizing the takeoff. Adjusting the material list based on what is readily available helps keep projects on schedule.
Another frequent error is overlooking fasteners, connectors, and additional structural reinforcements. Many takeoffs focus only on primary lumber, ignoring the necessary nails, screws, metal brackets, and adhesives that hold everything together. This results in unexpected shortages during construction. To avoid this, always include hardware and reinforcement materials in the takeoff and cross-check them with project specifications.
Failing to adjust for wood shrinkage and expansion can also cause problems, particularly in humid or dry environments. Wood naturally expands and contracts with changes in moisture levels, which can lead to structural misalignment if not accounted for. The solution is to apply climate-based adjustments when estimating lumber needs, selecting properly dried wood, and allowing for expansion gaps in certain structural components.
Lastly, relying only on manual calculations increases the risk of human error in measurements and estimations. Even experienced professionals can make mistakes when handling large amounts of data manually. A more efficient approach is to use Fondion’s digital takeoff software, which automates calculations, reduces errors, and allows for quick adjustments if project requirements change. Fondion streamlines material estimation ensures accuracy in measurements, and helps contractors manage procurement efficiently, keeping projects on schedule and within budget.
Conclusion
An accurate lumber takeoff is essential for avoiding material shortages, reducing waste, and keeping construction projects within budget. Errors in estimation can lead to costly delays and unnecessary expenses, making precise calculations essential.
By systematically reviewing construction plans, selecting the right lumber, and using standardized measurement techniques, you can improve accuracy and efficiency.
Incorporating digital takeoff tools ensures consistent material estimates, while regular pricing updates help maintain cost control. Standardizing the takeoff process minimizes miscalculations and ensures repeatable accuracy across projects. By following these best practices, contractors can streamline procurement, prevent costly errors, and optimize resource allocation, leading to a more efficient and profitable construction workflow.
Improve your Lumber takeoff process with Fondion
Fondion is a powerful construction takeoff software designed to streamline material estimation, automate calculations, and improve accuracy in project planning. By using Fondion, contractors can reduce errors, optimize workflows, and ensure better cost control. Whether you're managing a small project or a large-scale build, Fondion helps you stay efficient and on budget.
Start your free trial with Fondion today and simplify your lumber takeoff process.
FAQ
What Is a Lumber Takeoff?
A lumber takeoff is the process of estimating the quantity and types of wood materials required for a construction project. It involves reviewing plans, measuring dimensions, and calculating the necessary lumber to prevent material shortages and minimize waste. A well-executed takeoff ensures accurate budgeting and smooth project execution.
Why Is a Lumber Takeoff Important?
A lumber takeoff ensures the right amount of wood is ordered, avoiding shortages and excess materials that increase costs. It improves cost control, supports accurate bidding, and keeps projects on schedule. Proper material estimation reduces waste and ensures efficiency in procurement and construction.
How Can Construction Estimating Software Improve My Lumber Takeoff?
Good construction estimating software creates professional tender documents automatically and with the right content. This helps contractors win more projects and maintain better profit margins by clearly outlining what is included and excluded in the project scope. A well-documented takeoff enhances customer satisfaction by preventing misunderstandings and keeping projects within budget and on schedule.
What Are Common Mistakes to Avoid in Lumber Takeoff?
Some common mistakes include miscalculating material quantities, ignoring lumber grading, and not accounting for waste. Relying on outdated plans or manual calculations can lead to cost overruns and delays. Using accurate blueprints, factoring in waste percentages, and leveraging takeoff software help avoid these issues and improve accuracy.
What Features Should I Look for in a Lumber Takeoff Software?
Make sure that you don’t have to manually enter data into different systems, but rather, you can manage all information from a single system. If you are using various systems, the system you choose, like Fondion, should act as the master. This way, you only need to set up projects in one software, which then syncs with other tools. This allows you to accurately estimate and monitor costs while ensuring that you can learn from historical data about your true costs, optimizing your operations for profitability across different areas.